Leveraging AI for Enhanced Safety in Manufacturing Processes: A Comprehensive Guide
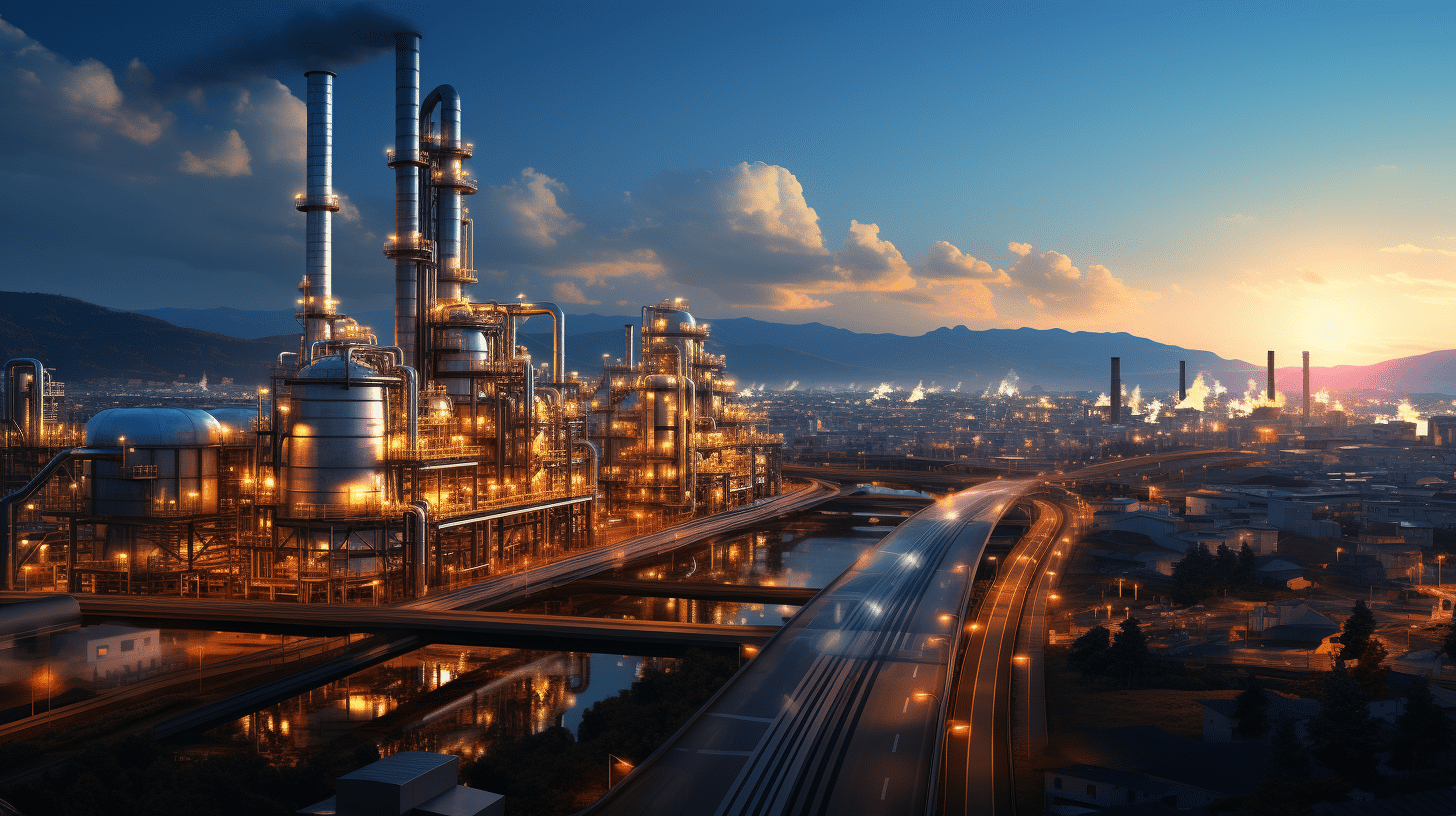
Table of Contents
Safety is a cornerstone in the manufacturing industry, especially in processes that involve potential hazards. With the digital transformation sweeping across sectors, Artificial Intelligence (AI) is playing a pivotal role in elevating safety standards. This article aims to serve as an exhaustive guide on AI in manufacturing process safety, offering actionable insights that go beyond existing literature on the subject.
The Evolution of Safety Measures in Manufacturing
Traditionally, safety in the manufacturing industry hinged on manual inspections, written protocols, and the vigilance of human workers. While these methods have their merits, they are susceptible to human error and are often reactive rather than proactive. The advent of AI technology is revolutionizing safety measures in the manufacturing industry, making them more data-driven, predictive, and reliable.
The Limitations of Traditional Methods
- Susceptibility to human error: The integration of AI in manufacturing processes can significantly reduce the susceptibility to human error by automating repetitive and critical tasks. Unlike humans, AI systems are not prone to fatigue, distractions, or inconsistencies, ensuring enhanced accuracy and reliability throughout the manufacturing process. By minimizing the potential for human errors, AI promotes safer working conditions, reduces production downtime, and enhances overall productivity.
- Time-consuming inspections: Traditional manual inspections in manufacturing processes can be time-consuming, leading to delays and inefficiencies. AI technology offers a solution by automating and expediting inspection procedures. AI-powered computer vision systems can quickly and accurately examine products, components, and equipment for deviations, defects, or abnormalities. This significantly reduces inspection time while maintaining high precision. Consequently, manufacturing processes can operate at optimal speed, meeting production targets, and avoiding potential safety hazards resulting from prolonged inspections.
- Limited data analysis capabilities: The integration of AI enables manufacturing processes to transcend limited data analysis capabilities by effectively managing and analyzing vast amounts of data. AI algorithms can extract meaningful insights from real-time sensor data, historical records, and other sources. By leveraging machine learning, these systems can identify patterns, detect anomalies, and predict potential safety risks. Such advanced data analysis capabilities ensure proactive identification and mitigation of safety hazards in manufacturing processes, empowering manufacturers to take preventative measures, ensuring worker safety, and improving overall process efficiency.
The Technological Shift
Introduction of sensors and IoT devices
The integration of sensors and IoT devices in manufacturing processes allows for continuous monitoring, data collection, and analysis, leading to improved safety measures and risk mitigation.
Data-driven decision-making through machine learning
Machine learning algorithms analyze vast amounts of data collected from manufacturing processes, enabling organizations to make informed, data-driven decisions for enhancing safety protocols.
Automated safety systems
AI-powered automated safety systems in manufacturing processes detect potential hazards, manipulate controls, and trigger safety protocols autonomously, ensuring a safer working environment for employees.
The Rise of AI in Manufacturing Safety
The manufacturing market is increasingly adopting AI solutions, with a projected growth rate of 30% in the next five years. This section will delve into various facets of AI applications in manufacturing safety, from real-time monitoring to predictive maintenance.
The Current Landscape
Statistical data on AI adoption in the manufacturing industry
AI adoption in the manufacturing industry is on the rise, with data showing its increasing prevalence. A report by the International Data Corporation (IDC) predicts that global spending on AI in manufacturing will reach $17.2 billion by 2024, representing a compound annual growth rate (CAGR) of 20.7%. This trend is driven by manufacturers’ recognition of AI’s potential to improve operational efficiency, enhance product quality, and ensure workplace safety.
The role of AI in different manufacturing sectors
In the automotive sector, AI plays a crucial role in improving process safety by enabling predictive maintenance, real-time monitoring of equipment, and identifying potential safety hazards. AI-driven technologies such as machine vision and robotics enhance worker safety by automating hazardous tasks and reducing human error.
Similarly, in the chemicals industry, AI contributes to manufacturing process safety by analyzing vast amounts of data from sensors and instruments. It can detect anomalies and deviations in real-time, enabling faster response to safety-critical situations. AI enhances risk assessment in the chemicals sector by identifying potential hazards and optimizing safety procedures.
Regarding food safety, AI plays a vital role in ensuring product quality and preventing contamination. It enables early detection of anomalies in production processes, allowing immediate action to be taken to avoid potential hazards. AI-powered sensors and cameras can identify foreign objects or impurities in food products, ensuring consumer safety and regulatory compliance.
Overall, AI’s impact on manufacturing process safety across automotive, chemicals, and food sectors is significant. Its ability to process vast amounts of data, detect patterns, and make intelligent decisions in real-time enhances safety measures and mitigates potential risks. This adoption of AI in manufacturing safety reflects a growing awareness of its transformative potential in improving industrial operations and protecting human lives.
The Future Outlook
Emerging AI Techniques in Safety
AI techniques are advancing rapidly in the manufacturing industry, offering opportunities to enhance safety measures. Here are some emerging AI techniques being applied to improve safety:
- Predictive Analytics: AI models can analyze historical data to identify patterns leading to safety incidents, enabling proactive actions to prevent accidents.
- Computer Vision: AI-powered cameras visually detect unsafe conditions, such as unauthorized personnel or incorrect use of protective equipment, ensuring compliance and preventing accidents.
- Natural Language Processing (NLP): NLP analyzes safety-related documents, identifying recurring issues, improving safety guidelines, and extracting insights from unstructured data.
- Sensor Data Analytics: AI algorithms monitor real-time sensor data, detecting anomalies and triggering alarms or shutdowns when safety limits are exceeded to prevent accidents.
The Potential for Generative AI to Revolutionize Safety Measures
Generative AI has the potential to revolutionize safety practices in manufacturing processes:
- Virtual Training Simulations: AI-generated simulations create realistic training environments, allowing workers to practice safety procedures and familiarize themselves with risks, reducing errors and increasing preparedness.
- Risk Assessment and Modeling: Generative AI analyzes manufacturing data, historical incidents, and safety guidelines, generating risk scenarios to evaluate potential impacts and implement targeted safety measures.
- Personalized Safety Recommendations: Generative AI provides personalized safety recommendations based on individual behavior and preferences, enhancing safety practices and awareness.
- Autonomous Safety Systems: Generative AI analyzes real-time data to generate algorithms that enable machines to make autonomous safety decisions, minimizing human errors and improving responsiveness.
The future outlook for AI in manufacturing process safety is promising. Advancements in AI techniques will lead to increased automation, precision, and effectiveness in safety measures. Generative AI will enable proactive risk assessment, personalized recommendations, and the development of autonomous safety systems, greatly enhancing manufacturing safety.
Key Benefits of AI in Manufacturing Safety
Real-Time Monitoring
AI algorithms can monitor manufacturing operations in real-time, offering immediate alerts for any safety hazards. This is a significant upgrade over traditional monitoring systems, which often involve time-lagged reporting.
How It Works
Real-time monitoring in AI-driven manufacturing process safety involves the collection of data using sensors and cameras. The gathered data is then analyzed in real-time using AI algorithms powered by machine learning. This analysis enables the immediate detection of any anomalies or safety hazards. Prompt alerts are generated to ensure quick response and mitigation. By combining data collection, AI analysis, and instant alerts, real-time monitoring enhances safety and minimizes risks in manufacturing processes.
Predictive Analytics and Maintenance
AI uses machine learning algorithms to analyze historical data for predicting potential future risks. Predictive maintenance can be scheduled if a machine shows signs of wear and tear, thereby enhancing worker safety and prolonging the production process.
The Power of Data
The power of data is evident in its ability to drive informed decision-making in manufacturing process safety and predictive maintenance. By collecting historical data and utilizing machine learning models, manufacturers can gain valuable insights, predict risks, and schedule proactive maintenance. This data-driven approach allows for optimized operational efficiency, improved process safety, and reduced downtime. Real-time monitoring and control systems integrated with data analysis further enhance the power of data, providing instant alerts and recommendations for process adjustments. Ultimately, leveraging the power of data in manufacturing processes leads to increased productivity and safety.
Automated Response Systems
AI-driven safety interlocks and emergency shutdown systems can react faster than human operators. These systems are particularly useful in high-risk environments like chemical manufacturing and food safety.
Safety Protocols
AI algorithms trigger safety mechanisms in manufacturing by continuously monitoring and analyzing data inputs. They detect hazards or abnormalities and activate safety measures such as machine shutdowns or alarms. The speed and efficiency of AI-driven response systems offer significant benefits. They enable instant recognition of dangers, minimizing response time and reducing the risk of accidents. AI can handle large amounts of real-time data, make quick decisions, and trigger appropriate safety mechanisms faster than human operators. These automated systems enhance manufacturing safety and create a safer working environment.
Employee Training and Awareness
AI can also play a crucial role in employee training. Virtual reality simulations powered by AI can provide real-world training scenarios, making the workforce better prepared for emergencies.
Training Modules
AI-powered training programs offer a new dimension in workplace safety education. Utilizing virtual reality simulations, these programs create realistic scenarios where employees can practice responding to potential hazards. This hands-on approach ensures that workers are not just theoretically prepared but also practically equipped to handle emergencies.
The Effectiveness of Virtual Reality Simulations in Workplace Safety
Virtual reality simulations have proven to be highly effective in enhancing workplace safety. These simulations, powered by advanced AI algorithms, provide a safe yet realistic environment for workers to practice emergency responses. Employees can engage in various scenarios that mimic real-life hazards, from equipment malfunctions to chemical spills. This immersive experience allows workers to better understand the potential risks and appropriate safety protocols, thereby improving their ability to respond effectively in actual emergency situations. The end result is a safer, more prepared workforce that contributes to the overall safety and operational efficiency of the manufacturing process.
Ethical Considerations
While AI offers numerous benefits, it also raises ethical questions, often referred to as the “Big Brother” concern. Employers must balance the need for safety monitoring with respect for employee privacy.
Ethical Guidelines
Data privacy laws
Data privacy laws refer to legal regulations and policies that protect the rights of individuals regarding the collection, storage, and use of their personal information. In the context of AI in manufacturing process safety, data privacy laws are important to ensure that sensitive information, such as employee health data or proprietary manufacturing processes, is adequately protected. Compliance with data privacy laws ensures transparency in data handling, helps build trust with employees, and mitigates the risk of data breaches or unauthorized access.
Employee consent for monitoring
Employee consent for monitoring refers to obtaining employees’ explicit and informed permission to collect and analyze their personal data in the manufacturing process. In an AI-enabled manufacturing environment, where sensors and devices gather data to ensure safety, monitoring may be necessary. However, obtaining employee consent helps address privacy concerns and promotes transparency. It allows employees to understand what data is being collected, how it is used, and ensures their rights and interests are respected while maintaining a safe working environment.
Transparency in data usage
Transparency in data usage is essential to enhance trust and accountability in the application of AI in manufacturing process safety. It involves clear communication about how data is collected, stored, processed, and used in manufacturing processes. By providing employees with transparency in data usage, organizations can assure them that their data is used solely for safety purposes and adheres to ethical standards. Transparency also enables employees to have a clear understanding of the benefits and potential risks associated with AI technologies, fostering a culture of openness and cooperation in the workplace.
Regulatory Compliance
AI in manufacturing safety is subject to various government regulations. Non-compliance can result in hefty fines and legal consequences. Companies must stay abreast of these regulations to avoid penalties.
Regulatory Bodies
- OSHA guidelines
- EPA regulations for environmental safety
- International standards like ISO
Management of Change (MOC) in AI-Driven Safety Measures
Implementing AI in existing safety protocols requires a well-planned Management of Change (MOC) process. This involves evaluating the impact of the new technology and communicating it effectively to all stakeholders.
The MOC Process
- Risk assessment
- Stakeholder communication
- Pilot testing and full-scale implementation
Communication Strategies
- Internal webinars to educate employees about the new AI systems
- Detailed guides and FAQs for easy reference
Conclusion
AI is not just a technological advancement; it’s a transformative tool that can significantly improve safety in manufacturing processes. As we move towards a more automated future, the role of AI in ensuring a safe and efficient manufacturing environment will only become more critical. By offering a holistic view of AI’s role in manufacturing safety, this article aims to serve as a one-stop resource for industry professionals. The future is here, and it’s automated, safer, and more efficient than ever before.
By covering these topics in depth, we hope to offer a resource that not only educates but also drives action towards adopting AI for a safer and more efficient manufacturing process.
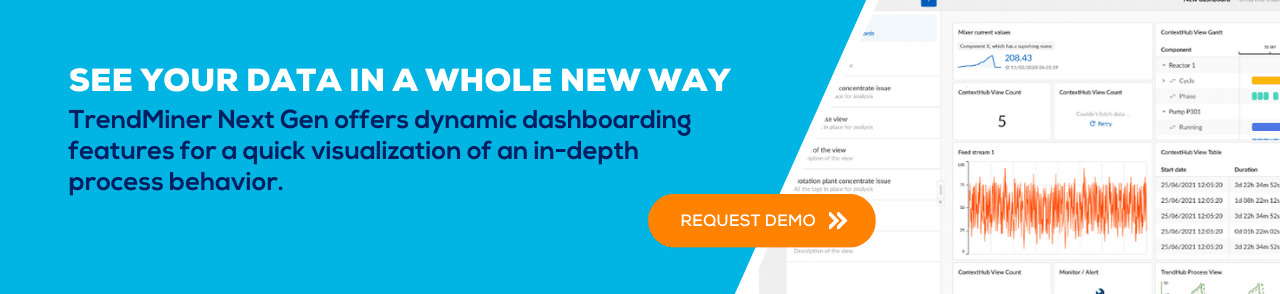
Unlock Your Industrial Potential
Discover how our analytics solutions can transform your process industry operations today.
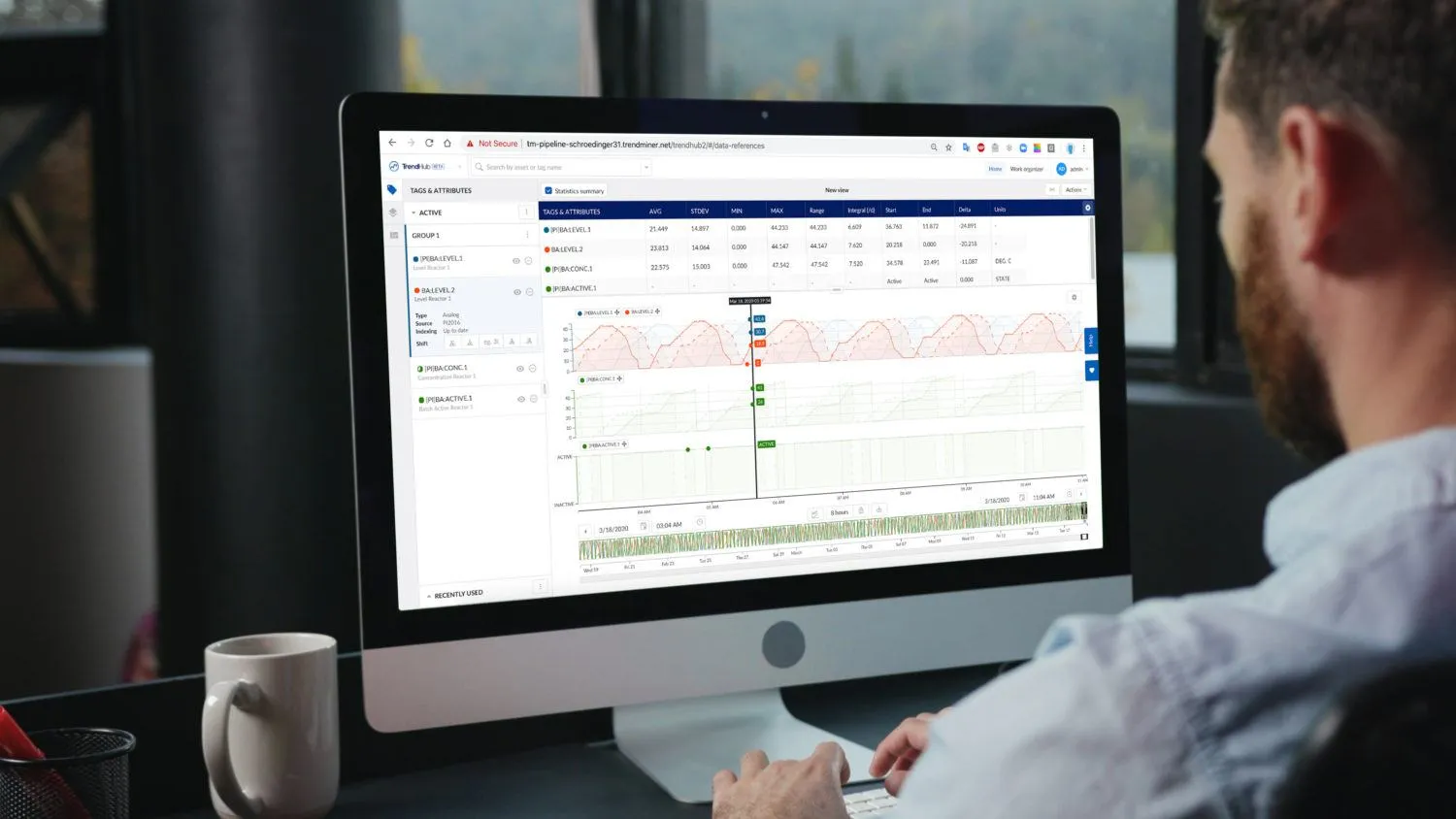
Subscribe to our newsletter
Stay up to date with our latest news and updates.
Latest Resources
Explore Our Newest Content to Maximize Your Operational Efficiency