Preventing Pump Resonance Failure for Enhanced Reliability Saves Up To $360k Per Equipment Per Day
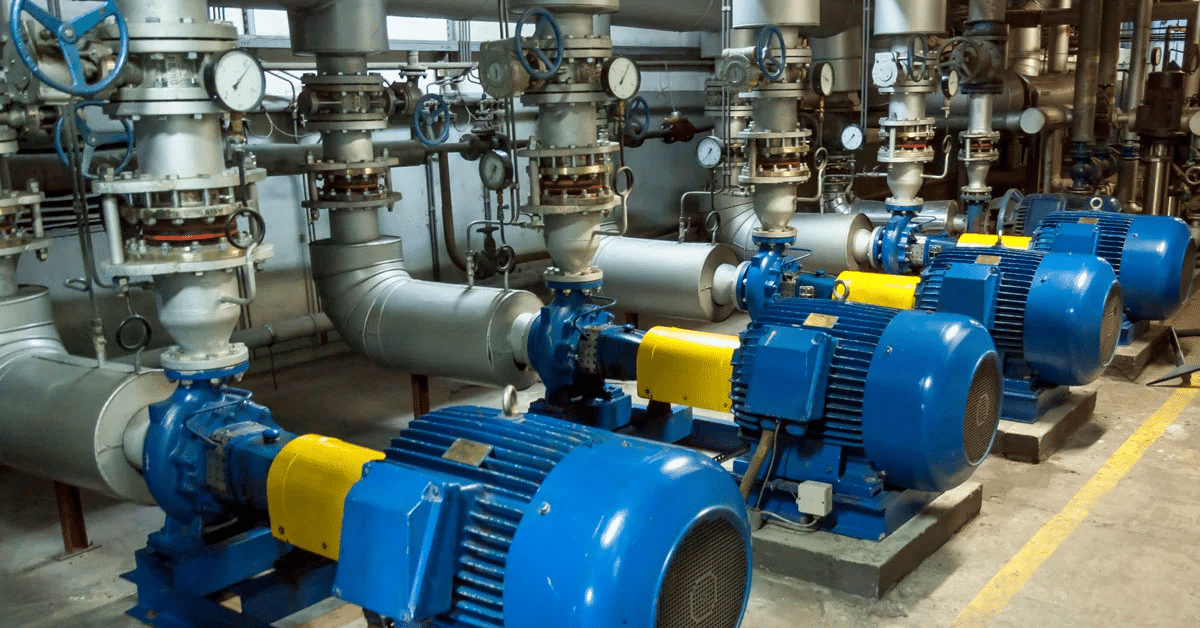
Situation
In crude oil processing units, pumps such as 23P31, 23P1, and 23P2 are critical to maintaining continuous operations. However, these pumps are susceptible to resonance at certain flow rates, which can lead to severe operational issues. When resonance occurs, it raises the risk of seal failure, loss of containment, bearing collapse, and rotor-to-casing rub. These problems can cause extended downtime, significantly impacting production and leading to costly repairs.
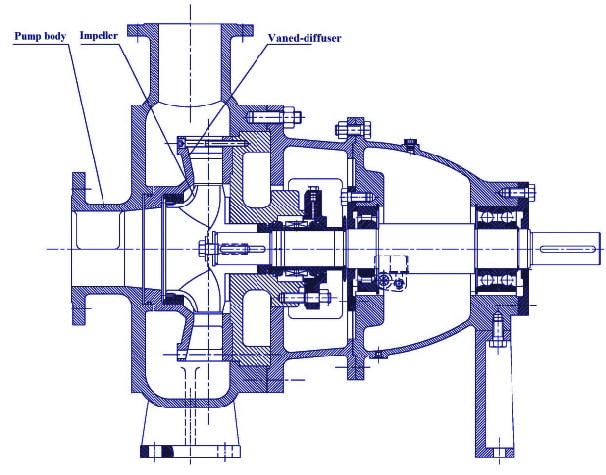
Problem
The primary challenge arises when the pumps operate at specific flow rates that trigger resonance. This resonance can lead to catastrophic failures, including seal damage, bearing failures, and potential rotor-to-casing contact. Such failures not only disrupt operations but can also result in significant financial losses due to repair costs and lost production time. The risk is particularly high when flow conditions are not balanced, as this can exacerbate the resonance and the associated mechanical failures.
Solution
To address this critical issue, a new monitoring approach has been developed. This solution involves creating a new view that visualizes the key tags for each pump, enabling detailed tracking and analysis of their performance.
By performing value-based searches, operators can identify different events where pump 23P31 operates in a single pump mode at approximately 500 m³/h. This is complemented by using visual comparison in trends, supported by statistical analysis through a statistic table. For instance, if pump 23P31 operates at 450 m³/h, it induces vibrations in pump 23P1, leading to chronic bearing damage. Similarly, at 550 m³/h, it affects pump 23P2 in the same way.
This data-driven approach allows for the early detection of resonance conditions and the implementation of corrective actions before severe damage occurs.
Results
The implementation of this solution offers substantial benefits:
- Cost Savings: Avoiding bearing damage and seal failure, saving between $5,000 to $60,000 depending on the severity.
- Production Continuity: Preventing production slowdowns that could cost $250,000 to $300,000 per day if multiple pumps fail.
- Increased Uptime: Extending production time by 1 to 21 days, depending on the repair actions avoided.
- Enhanced Reliability: Overall reduction in maintenance costs and production losses, leading to more reliable operations.
Overall, this proactive monitoring and analysis system not only enhances operational reliability but also significantly reduces maintenance costs and production losses.
Situation
In crude oil processing units, pumps such as 23P31, 23P1, and 23P2 are critical to maintaining continuous operations. However, these pumps are susceptible to resonance at certain flow rates, which can lead to severe operational issues. When resonance occurs, it raises the risk of seal failure, loss of containment, bearing collapse, and rotor-to-casing rub. These problems can cause extended downtime, significantly impacting production and leading to costly repairs.
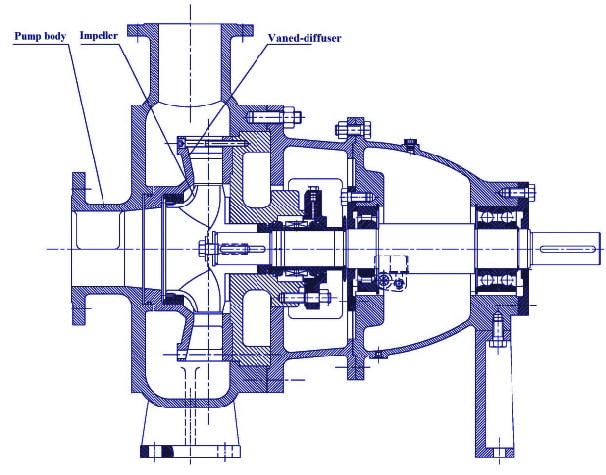
Problem
The primary challenge arises when the pumps operate at specific flow rates that trigger resonance. This resonance can lead to catastrophic failures, including seal damage, bearing failures, and potential rotor-to-casing contact. Such failures not only disrupt operations but can also result in significant financial losses due to repair costs and lost production time. The risk is particularly high when flow conditions are not balanced, as this can exacerbate the resonance and the associated mechanical failures.
Solution
To address this critical issue, a new monitoring approach has been developed. This solution involves creating a new view that visualizes the key tags for each pump, enabling detailed tracking and analysis of their performance.
By performing value-based searches, operators can identify different events where pump 23P31 operates in a single pump mode at approximately 500 m³/h. This is complemented by using visual comparison in trends, supported by statistical analysis through a statistic table. For instance, if pump 23P31 operates at 450 m³/h, it induces vibrations in pump 23P1, leading to chronic bearing damage. Similarly, at 550 m³/h, it affects pump 23P2 in the same way.
This data-driven approach allows for the early detection of resonance conditions and the implementation of corrective actions before severe damage occurs.
Results
The implementation of this solution offers substantial benefits:
- Cost Savings: Avoiding bearing damage and seal failure, saving between $5,000 to $60,000 depending on the severity.
- Production Continuity: Preventing production slowdowns that could cost $250,000 to $300,000 per day if multiple pumps fail.
- Increased Uptime: Extending production time by 1 to 21 days, depending on the repair actions avoided.
- Enhanced Reliability: Overall reduction in maintenance costs and production losses, leading to more reliable operations.
Overall, this proactive monitoring and analysis system not only enhances operational reliability but also significantly reduces maintenance costs and production losses.
Download now
Subscribe to our newsletter
Stay up to date with our latest news and updates.
Other Webinars on demand
Explore Our Newest Content to Maximize Your Operational Efficiency
Other Resources
Explore Our Newest Content to Maximize Your Operational Efficiency