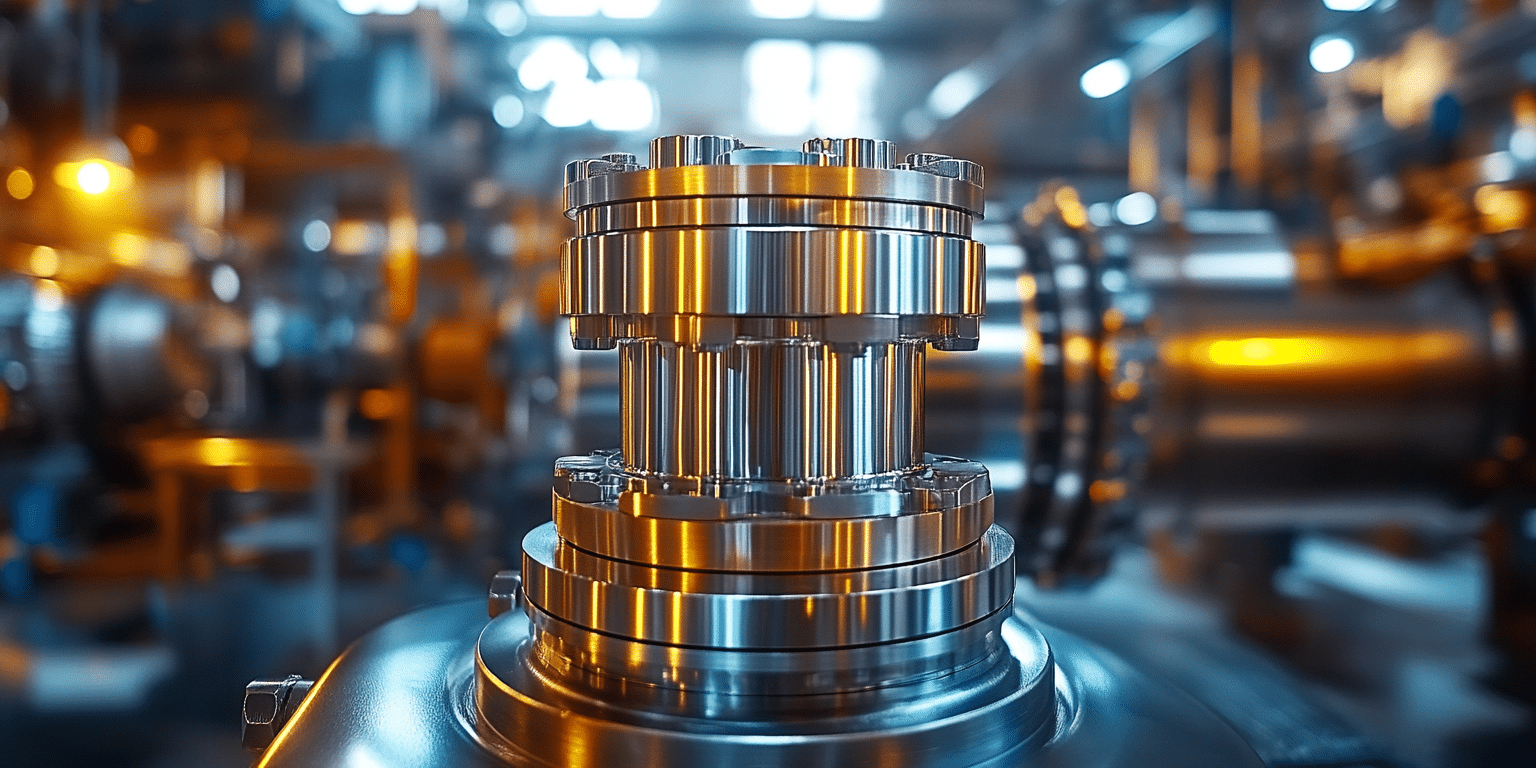
Situation
Mechanical seals are vital components in many process industries, particularly in the oil and gas sector. These seals play a crucial role in maintaining the safety and integrity of operations. When mechanical seals fail, they can pose significant risks to both safety and the environment, potentially leading to severe operational disruptions. Given the critical importance of fully operational seals, monitoring their condition is essential to ensure the safety and continuity of operations.
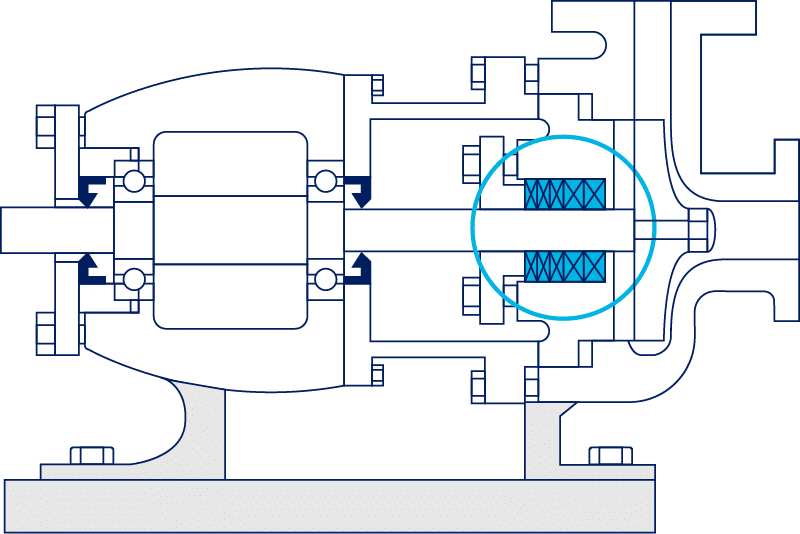
Problem
The failure of mechanical seals presents several key challenges.
First, there are significant safety and environmental threats. If seals fail, they can lead to leaks, which pose severe safety risks and environmental hazards. This can result in not only operational setbacks but also regulatory and compliance issues.
Second, without continuous monitoring, it becomes challenging to assess the real-time status of seals, which makes it difficult to preempt potential issues. This uncertainty can lead to unexpected failures, resulting in downtime and maintenance emergencies.
Lastly, the absence of adequate monitoring practices can lead to reduced uptime and a shorter lifespan for the seals. This not only disrupts operations but also incurs additional costs due to frequent repairs and replacements.
Solution
To address these issues, a comprehensive preventive monitoring system has been set up. This system continuously tracks the condition of mechanical seals, enabling operational teams to take proactive measures before any risks escalate. By identifying the thresholds for undesirable pressure changes, the system operationalizes these findings into a live monitor, ensuring that the seals’ status is always up to date.
The real-time dashboard provides an overview of all operational seals, alerting the team to any anomalies such as unexpected pressure changes. This allows for timely interventions, reducing the likelihood of failures.
Furthermore, by using real-time data, maintenance can be scheduled proactively, which helps to extend the seals’ lifespan and reduce the frequency of operational disruptions.
Results
Proactive monitoring for enhanced operational safety and efficiency results In $100k+ savings per year per refinery.
- Enhanced Safety: Preventive monitoring significantly reduces the risk of environmental and safety incidents.
- Operational Efficiency: Real-time monitoring and analysis contribute to fewer disruptions and longer seal lifespans, leading to increased uptime and reduced maintenance costs.
- Improved Decision-Making: The availability of real-time data empowers operational teams to make informed decisions quickly, optimizing overall process performance.
Situation
Mechanical seals are vital components in many process industries, particularly in the oil and gas sector. These seals play a crucial role in maintaining the safety and integrity of operations. When mechanical seals fail, they can pose significant risks to both safety and the environment, potentially leading to severe operational disruptions. Given the critical importance of fully operational seals, monitoring their condition is essential to ensure the safety and continuity of operations.
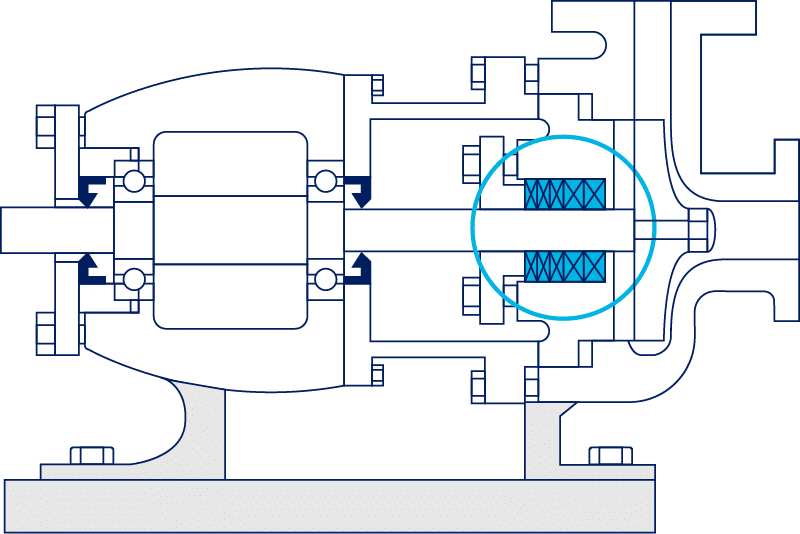
Problem
The failure of mechanical seals presents several key challenges.
First, there are significant safety and environmental threats. If seals fail, they can lead to leaks, which pose severe safety risks and environmental hazards. This can result in not only operational setbacks but also regulatory and compliance issues.
Second, without continuous monitoring, it becomes challenging to assess the real-time status of seals, which makes it difficult to preempt potential issues. This uncertainty can lead to unexpected failures, resulting in downtime and maintenance emergencies.
Lastly, the absence of adequate monitoring practices can lead to reduced uptime and a shorter lifespan for the seals. This not only disrupts operations but also incurs additional costs due to frequent repairs and replacements.
Solution
To address these issues, a comprehensive preventive monitoring system has been set up. This system continuously tracks the condition of mechanical seals, enabling operational teams to take proactive measures before any risks escalate. By identifying the thresholds for undesirable pressure changes, the system operationalizes these findings into a live monitor, ensuring that the seals’ status is always up to date.
The real-time dashboard provides an overview of all operational seals, alerting the team to any anomalies such as unexpected pressure changes. This allows for timely interventions, reducing the likelihood of failures.
Furthermore, by using real-time data, maintenance can be scheduled proactively, which helps to extend the seals’ lifespan and reduce the frequency of operational disruptions.
Results
Proactive monitoring for enhanced operational safety and efficiency results In $100k+ savings per year per refinery.
- Enhanced Safety: Preventive monitoring significantly reduces the risk of environmental and safety incidents.
- Operational Efficiency: Real-time monitoring and analysis contribute to fewer disruptions and longer seal lifespans, leading to increased uptime and reduced maintenance costs.
- Improved Decision-Making: The availability of real-time data empowers operational teams to make informed decisions quickly, optimizing overall process performance.
Download now
Subscribe to our newsletter
Stay up to date with our latest news and updates.
Other Webinars on Demand
Press Play on Operational Improvement
Other Resources
Explore Our Newest Content to Maximize Your Operational Efficiency