Mastering Operations Performance Management: A Comprehensive Guide
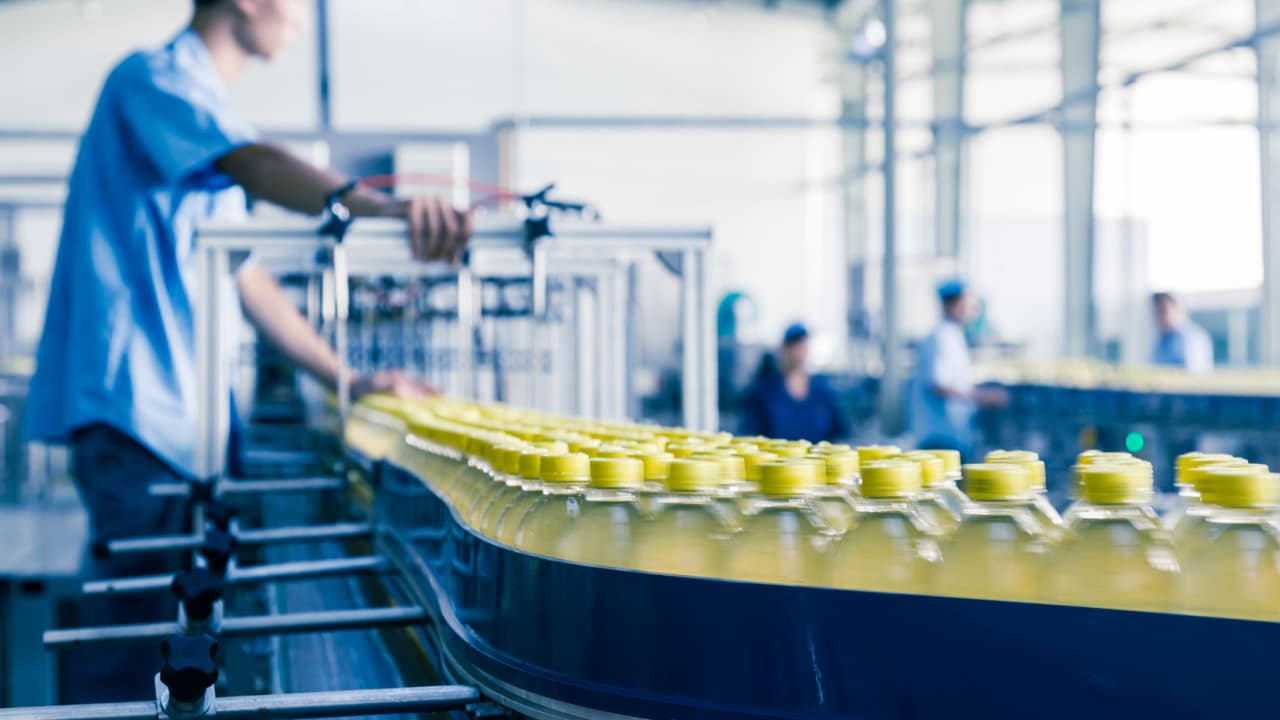
Table of Contents
Introduction
Operations Performance Management (OPM) is a fundamental aspect of modern businesses, specifically in the manufacturing industry. Efficiently managing and improving the performance of operational processes within an organization is crucial for enhancing productivity, efficiency, and overall success. In this section, we will explore the definition of OPM and highlight its significance.
Definition of Operations Performance Management (OPM)
Operations Performance Management is a comprehensive process that involves effectively managing the performance of operational activities within a business to achieve strategic goals. It encompasses the measurement, analysis, and improvement of various operational processes such as production, supply chain management, quality control, and customer service. The primary objective of OPM is to optimize these processes to ensure maximum efficiency, effectiveness, and profitability.
Importance of OPM in modern businesses
In today’s fiercely competitive business environment, the adoption of effective OPM practices is vital for the success and sustainability of manufacturing companies. By identifying and addressing operational inefficiencies, OPM enables organizations to streamline their processes and fulfill customer demands promptly. Additionally, effective OPM provides valuable insights and data that enable managers to make informed decisions and allocate resources efficiently.
Furthermore, OPM plays a pivotal role in driving continuous improvement within manufacturing operations. By establishing performance metrics, setting targets, and monitoring progress, organizations can identify areas for enhancement and take corrective actions to optimize performance. This proactive approach prevents issues from escalating and helps businesses stay ahead of the competition.
Overall, the significance of OPM lies in achieving operational excellence, optimizing resource utilization, maintaining quality standards, and meeting customer expectations. It allows manufacturing companies to adapt swiftly to changing market conditions, enhance profitability, and sustain long-term success in an increasingly dynamic business environment. As technology advances, advanced industrial analytics is emerging as a powerful tool in OPM, enabling organizations to gain actionable insights, identify patterns, and make data-driven decisions to further optimize their operational performance.
The Evolution of Performance Management
The evolution of performance management has been driven by the need for a more strategic and proactive approach to managing performance in the manufacturing industry. Traditional methods focused on annual reviews and disciplinary actions, but they failed to address the strategic goals of organizations and had limited impact on overall performance.
The shift towards modern Operational Performance Management (OPM) was necessary to address the increased complexity of business operations and the need to stay competitive in a rapidly changing market. OPM goes beyond evaluating employees and becomes an integral part of organizational strategy.
OPM revolves around aligning business units, fostering ongoing communication processes, measuring and developing individual and team performance, and linking performance to strategic goals. Alignment of business units ensures that everyone works towards a common objective, with clear and measurable performance targets set for each unit. Ongoing communication processes facilitate feedback and collaboration, creating a culture of continuous improvement.
Measuring and developing individual and team performance is a crucial aspect of OPM. By implementing performance indicators and conducting regular evaluations, organizations can identify areas for improvement and provide support for enhancing performance. This enables employees to grow and contribute to the overall success of the organization.
Aligning performance with strategic goals ensures that employees understand the bigger picture and work towards it. This promotes a sense of purpose and ownership, as everyone’s efforts directly contribute to the achievement of long-term objectives.
Core Components of Operational Performance Management
Alignment of business units
Successful operational performance management relies on the alignment of different business units within an organization. Each unit should have a clear understanding of the organization’s overall goals and objectives and how their individual performance contributes to the achievement of those goals. This alignment fosters a sense of teamwork and collaboration, ensuring everyone is working towards a common purpose.
Ongoing communication processes
Open and regular communication channels between managers and employees are vital for effective operational performance management. These channels allow for the exchange of information, clarification of expectations, and addressing any issues or concerns that may arise. Communication also facilitates the sharing of feedback, both positive and constructive, which is essential for continuous improvement and development.
Measuring and developing individual and team performance
Measuring individual and team performance plays a crucial role in operational performance management. Clear and objective performance metrics should be established to evaluate employees’ work and contributions. Regular performance reviews and evaluations provide opportunities for feedback, recognition, and identifying areas for improvement. Additionally, development plans can be implemented to help employees enhance their skills and capabilities, enabling them to reach their full potential.
Aligning performance with strategic organizational goals
Operational performance management should be closely aligned with an organization’s strategic goals and objectives. It is crucial to ensure that individual and team performance goals are directly linked to the overall strategic direction of the organization. This alignment focuses efforts on achieving desired outcomes and ensures effective allocation of resources to support strategic priorities.
By aligning business units, fostering ongoing communication, measuring and developing individual and team performance, and aligning performance with strategic goals, operational performance management enables organizations to optimize their operations and achieve better outcomes. It cultivates a culture of high performance, accountability, and continuous improvement, resulting in increased productivity, efficiency, and ultimately, business success.
The Whole Work System of Performance Management
Job Definition and its Significance
In the manufacturing industry, a clear job definition is crucial for effective Operations Performance Management (OPM). By outlining the specific tasks and expected standards, a well-defined job description enables relevant and aligned performance metrics. This clarity reduces ambiguities and ensures that employees understand their responsibilities, facilitating accurate performance assessments.
The Lifecycle of an Employee within an Organization
An employee’s journey in a manufacturing firm spans from recruitment to retirement or exit. Each phase of this lifecycle has its own set of performance metrics. For example, during onboarding, the focus may be on how quickly a new hire adapts to the company’s processes. As employees grow, metrics shift towards efficiency, quality of work, and leadership capabilities. OPM ensures that performance metrics evolve alongside employees’ changing roles and responsibilities.
The Role of Supervisors and Continuous Feedback
Supervisors play a pivotal role in the OPM system, acting as the bridge between the workforce and higher management. They communicate, ensure understanding of performance standards, and provide continuous feedback. This feedback helps employees identify areas for improvement and growth. In the dynamic manufacturing environment, where processes and technologies continually evolve, regular feedback is vital. It keeps employees updated with best practices and aligned with organizational performance goals. Supervisors, through continuous feedback, foster a culture of continuous improvement, driving individual and organizational success.
Benefits of Effective Operations Performance Management
Achieving Core Business Goals
In order for a process manufacturing industry to thrive, it is essential to effectively align its operations with its core business goals. This is where Operations Performance Management (OPM) plays a significant role. By implementing OPM strategies and practices, companies can ensure that their operational activities are directed towards achieving the desired outcomes. Clear goal-setting and aligning performance metrics with strategic objectives enable organizations to optimize their operations and drive success.
Enhancing Employee Satisfaction and Retention
Employee satisfaction is a crucial aspect of any organization’s success, and effective OPM contributes to this in several ways. When OPM is implemented, employees gain a clear understanding of how their work contributes to the overall goals of the company. This sense of purpose and connection to the bigger picture enhances employee satisfaction. Additionally, ongoing communication processes in OPM create a platform for employees to receive feedback and recognition, fostering a positive work culture. When employees feel valued and appreciated, they are more likely to stay with the organization, leading to increased retention rates.
Boosting Organizational Productivity and Efficiency
One of the primary benefits of effective OPM in the process manufacturing industry is the improvement of organizational productivity and efficiency. By measuring and developing individual and team performance, companies can identify areas for improvement and implement targeted strategies. OPM allows organizations to set key performance indicators (KPIs) and monitor their progress, enabling them to make data-driven decisions. By optimizing internal processes and addressing performance issues promptly, companies enhance overall efficiency, leading to increased productivity.
Challenges in Implementing OPM
Common Pitfalls and How to Avoid Them
Implementing Operational Performance Management (OPM) in the process manufacturing industry can come with its fair share of challenges. However, by understanding these common pitfalls and implementing effective strategies, organizations can overcome hurdles and ensure successful OPM implementations.
Lack of Leadership Support and Alignment:
One of the major challenges in implementing OPM is the lack of support and alignment from top-level leadership. Without the commitment and buy-in from key executives and managers, the implementation may fall short of achieving its objectives. To overcome this challenge, it is crucial to educate leaders about the benefits of OPM and demonstrate its alignment with organizational goals and objectives.
Inadequate Data Availability and Quality:
Another challenge organizations face is the availability and quality of data required for effective performance management. Without accurate and reliable data, it becomes difficult to measure and monitor performance effectively. To address this challenge, organizations should invest in robust data collection systems, ensure data integrity, and establish clear processes for data validation and verification.
Resistance to Change:
Implementing OPM often requires changes in existing processes, workflows, and systems. This can lead to resistance from employees comfortable with the status quo. To overcome resistance to change, organizations should emphasize the benefits of OPM, provide employees with training and support, and involve them in the implementation process. By fostering a culture of continuous improvement and involving employees in decision-making, organizations can mitigate resistance and encourage buy-in.
Lack of Clear Communication and Goals:
Without clear communication and well-defined goals, OPM implementations can easily falter. It is essential to communicate the purpose, benefits, and expected outcomes of the OPM initiative to all stakeholders. Additionally, setting clear and achievable goals, incorporating key performance indicators (KPIs), and monitoring progress regularly can help maintain focus and drive performance improvement.
Insufficient Resources and Infrastructure:
OPM requires adequate resources, including technology and infrastructure, to support effective performance management. Limited resources can hinder the implementation process and compromise its success. Organizations should allocate sufficient financial and technological resources to support OPM initiatives. This may include investing in suitable performance management software, upgrading infrastructure, and providing necessary training and support to employees.
Case Studies of Failed OPM Implementations
Learning from the failures of others can serve as a valuable guide when implementing OPM. Exploring real-life case studies of failed OPM implementations can provide insights into the challenges organizations faced and the steps they could have taken to avoid those pitfalls. By studying these case studies, organizations can identify potential roadblocks and develop strategies to address them proactively.
Best Practices in Operational Performance Management
The success of any organization heavily depends on its ability to effectively manage operational performance. By implementing best practices in operational performance management (OPM), companies can streamline their processes, enhance productivity, and achieve their strategic goals. In this section, we will explore three key best practices that can contribute to the success of OPM initiatives.
Tools and technologies aiding OPM:
The use of advanced tools and technologies is crucial in optimizing operational performance. By leveraging cutting-edge software and automation solutions, businesses can monitor and measure performance indicators in real-time, identify bottlenecks, and make informed decisions. These tools enable organizations to track key performance metrics, such as cycle time, production yield, and equipment downtime, providing valuable insights for operational improvement.
Role of data analytics in performance measurement
Data analytics plays a pivotal role in OPM by providing organizations with actionable insights for performance measurement and improvement. By leveraging data from various sources, including production systems, sensors, and customer feedback, companies can uncover patterns, trends, and opportunities for enhancement. Analyzing this data allows organizations to identify areas of underperformance, optimize processes, and make data-driven decisions to achieve operational excellence.
Continuous training and development programs:
Investing in the training and development of employees is another fundamental best practice in OPM. Providing regular training sessions and workshops allows employees to acquire new skills, improve their performance, and stay updated with the latest industry trends. Continuous development programs also foster a culture of innovation and excellence, leading to increased employee engagement and motivation. When employees are equipped with the necessary knowledge and skills, they can contribute to the overall operational performance of the organization.
The Future of Operations Performance Management
Predictive Analytics and AI in OPM
One of the key drivers shaping the future of operations performance management (OPM) in the process manufacturing industry is the integration of predictive analytics and artificial intelligence (AI). These technologies have the potential to revolutionize the way organizations monitor and optimize their operations.
Predictive analytics utilizes historical data and machine learning algorithms to identify trends, patterns, and outliers. By analyzing past performance data, organizations can make informed predictions about future outcomes. This enables them to proactively address potential bottlenecks, optimize resource allocation, and identify areas for improvement. With predictive analytics, process manufacturers can achieve higher levels of efficiency and performance, leading to cost savings and better customer satisfaction.
AI, on the other hand, takes data analysis a step further by enabling machines to learn from experience and make autonomous decisions. AI-powered systems can identify operational inefficiencies, discover correlations between variables, and provide actionable insights in real-time. This empowers organizations to make data-driven decisions, automate routine tasks, and optimize their processes. From predictive maintenance to demand forecasting, AI has the potential to transform OPM and unlock new levels of operational excellence.
The Role of Remote Work and Digital Transformation
The rise of remote work and the accelerated digital transformation of industries are also influencing the future of OPM. With advancements in technology, remote work has become more feasible and widely adopted. This shift has implications for OPM, as organizations need to establish robust digital systems and platforms to monitor and manage performance from remote locations.
Digital transformation, including the adoption of cloud-based systems, data analytics tools, and collaboration platforms, is fundamental for effective OPM in a distributed work environment. Real-time data sharing, virtual collaboration, and seamless communication across teams are essential for monitoring and optimizing performance in a remote setup. By embracing digital transformation, process manufacturers can ensure continuous improvement, foster innovation, and maintain operational efficiency, regardless of geographical constraints.
Integrating OPM with Other Business Systems
To achieve a holistic view of operations and drive overall business performance, integrating OPM with other critical business systems is crucial. By aligning OPM with supply chain management, customer relationship management, and financial systems, organizations can gain actionable insights and make data-driven decisions.
Integration allows for improved coordination and communication across departments. For example, by connecting OPM with supply chain management, organizations can optimize inventory levels, ensure timely delivery, and minimize disruptions. By integrating with customer relationship management, OPM can enable better customer satisfaction tracking, identify areas for improvement, and enhance the overall customer experience.
Conclusion
Performance management is a crucial aspect of running a successful business in the process manufacturing industry. In this section, we will recap the significance of mastering Operations Performance Management (OPM) and encourage businesses to adopt a proactive approach to performance management.
Mastering OPM is essential for organizations to thrive in today’s competitive market. By effectively managing operations performance, companies can ensure that they are meeting their core business goals and objectives. OPM provides a framework for aligning individual and team performance with strategic organizational goals, enabling businesses to optimize their resources and drive success.
Another significant benefit of implementing OPM is the enhancement of employee satisfaction and retention. When employees understand how their individual contributions align with the overall goals of the organization, they feel a sense of purpose and are more motivated to perform at their best. This leads to higher levels of job satisfaction, increased retention rates, and a positive work culture.
Furthermore, effective OPM practices can significantly improve organizational productivity and efficiency. By continuously measuring and developing individual and team performance, companies can identify areas for improvement and take corrective action to enhance their operational processes. OPM ensures that employees have clear goals, receive continuous feedback from their supervisors, and participate in ongoing training and development programs. This results in greater efficiency and higher-quality outputs.
In conclusion, mastering Operations Performance Management is paramount for businesses in the process manufacturing industry. By aligning performance with strategic organizational goals, organizations can achieve core business objectives, enhance employee satisfaction and retention, and boost productivity and efficiency. We encourage businesses to adopt a proactive approach to performance management and leverage the best practices and tools available to them. With a proactive and strategic approach to OPM, companies can position themselves for long-term success in an ever-evolving industry.
Unlock Your Industrial Potential
Discover how our analytics solutions can transform your process industry operations today.
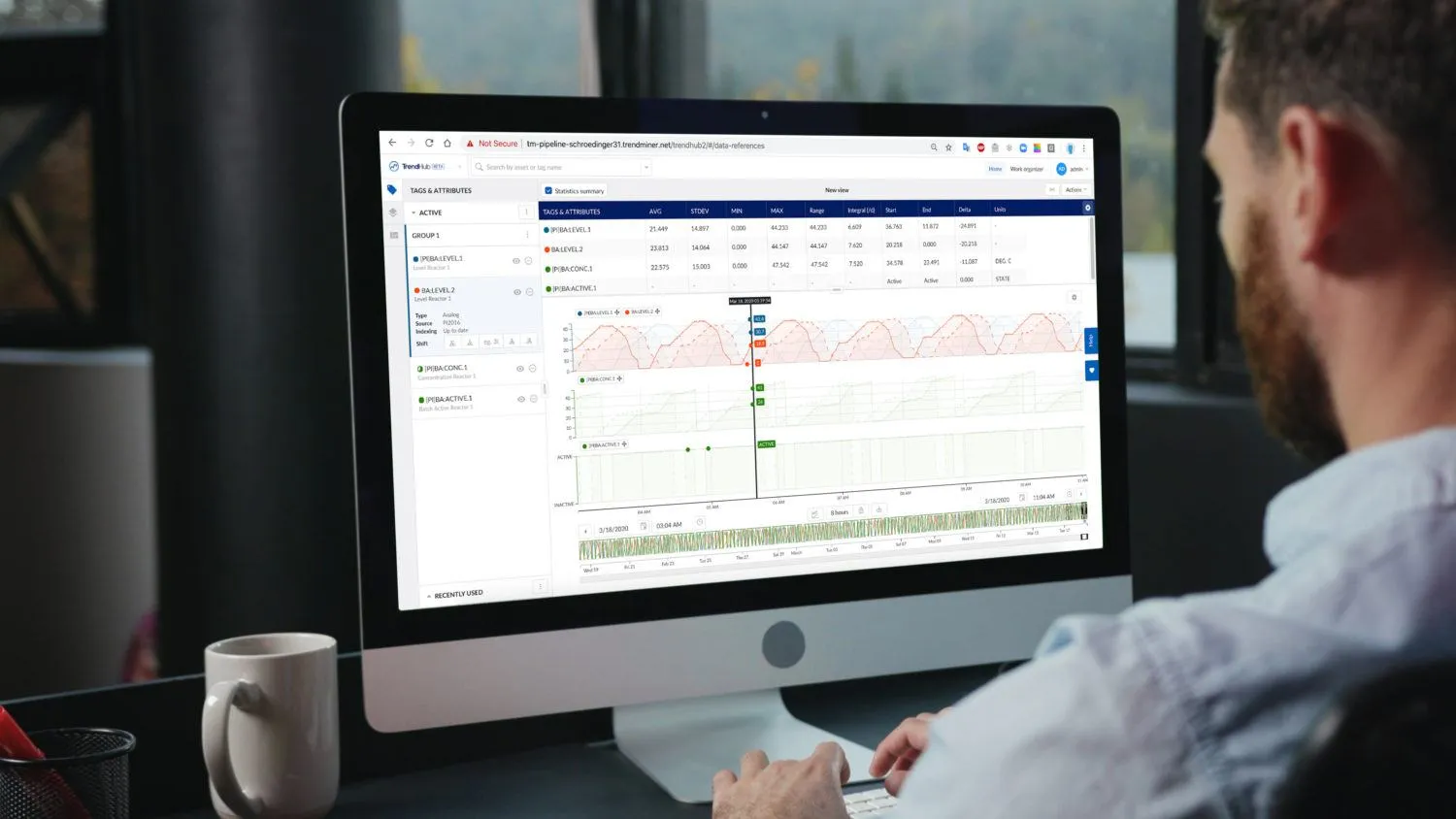
Subscribe to our newsletter
Stay up to date with our latest news and updates.
Latest Resources
Explore Our Newest Content to Maximize Your Operational Efficiency