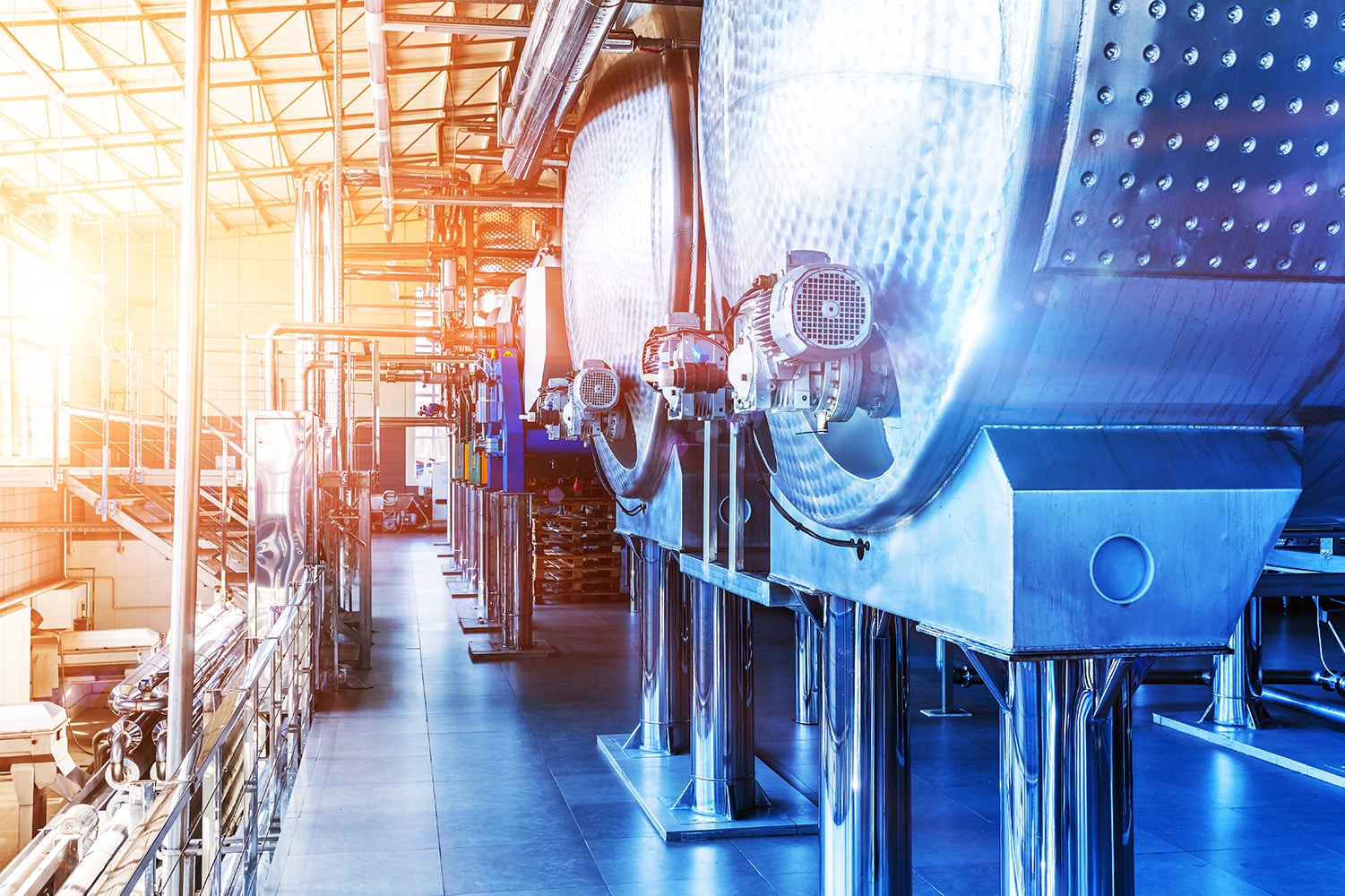
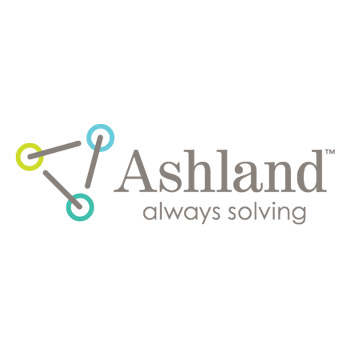
About Ashland
ASHLAND, a $5 billion US based provider of speciality chemical solutions is shifting the company focus from the construction market to the pharmaceutical market.
In this success story, Jan Meireleire, Engineering Manager at Ashland explains how the plant in Doel, Belgium benefits greatly from implementing TrendMiner’s self-service industrial analytics software – including solving previously unsolvable production issue, enhancing their reliability, quality and profitability, and increasing GMP production throughput.
Their Journey
Ashland consists of two commercial units: performance materials and specialty ingredients. Through the years, the plant in Belgium slowly changed their product towards use for personal care and pharmaceuticals.
New market sparks new challenges. A shift towards realizing a higher added value and a lower throughput of the product was needed, as well as maintaining a highly controlled process.
Next to that, manufacturing for the pharmaceuticals market means complying to strict regulations and control regarding product quality.
Solution & Implementation
Self-service industrial analytics proved to be the solution that could help Ashland to analyze and understand their data better and leverage it to profit from digitalization. How? Historical data is brought to AspenTech software on a dedicated server. TrendMiner’s self service analytics platform is put on top of it, which enables engineers to analyze and monitor the data.
Use Case 1
Data analysis: stabilize production by thinking outside the (data) box
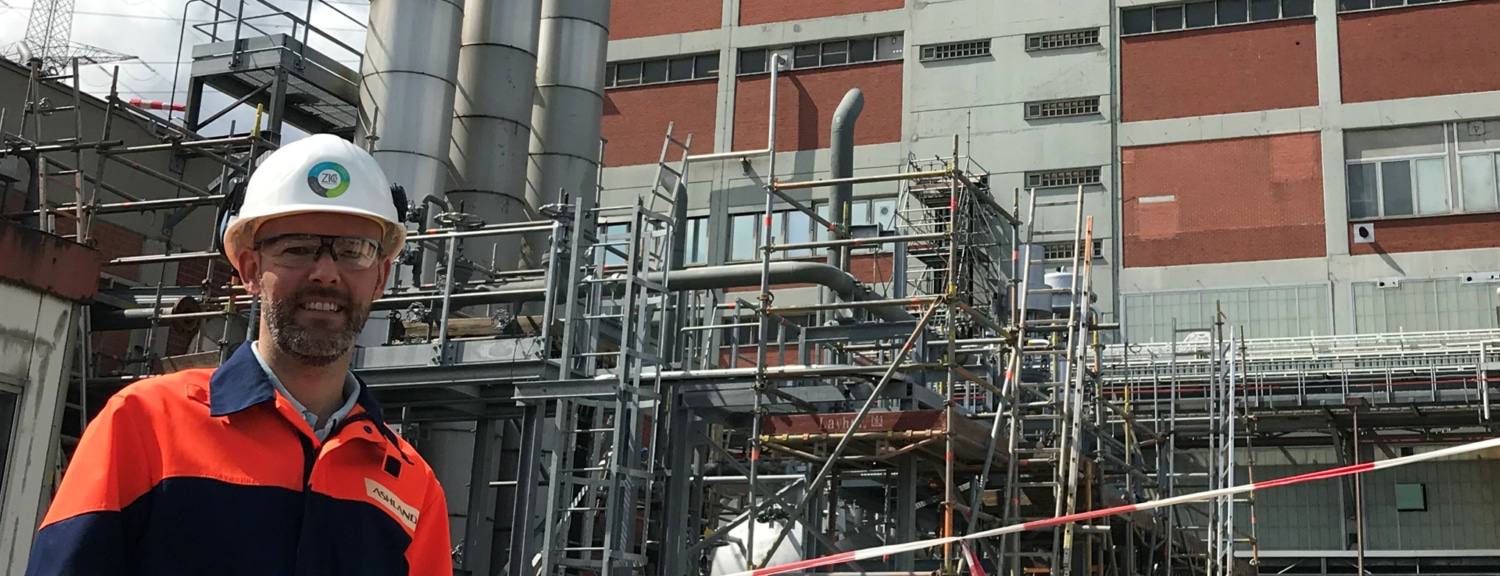
In this particular case, TrendMiner identified the most stable runs of production by filtering out data from some specific products. While all the relevant parameters in these production runs turned out to be stable, searching the entire database showed factors of influence at the very beginning of the process.
These so-called influence factors assisted with root cause analysis, helping the engineers to determine unknown correlations upstream.
With help from the software, process engineers didn’t need to extract tons of data and figures into an Excel sheet. The time that process engineers manipulate data is greatly reduced, while production is further stabilized.
Use Case 2
Data monitoring: run a smooth plant
The monitoring capabilities within TrendMiner enables process and production engineers to raise certain ‘red flags’ in time, and prevent incidents from happening in the future. Based on patterns, engineers can highlight Golden Fingerprints and are notified when an incident occurs.
At one given point in time, the process engineering group was warned about a specific event. Further analysis showed it had occurred several times the past. Instead of manually analysing data, data monitoring from TrendMiner software helped solve the incident, as well as preventing similar future ones. This is an important step towards a highly controlled process.
Benefits
Implementing TrendMiner’s self-service industrial analytics platform has helped Ashland to solve previously unsolvable production issues and enhance quality. Also, the on-target production of GMP products increased from 70% to 95%.
In this video Kobe Debie, Process Engineer at Ashland explains how TrendMiner helps to continuously improve their production process for both their continuous and batch production.
About Ashland
ASHLAND, a $5 billion US based provider of speciality chemical solutions is shifting the company focus from the construction market to the pharmaceutical market.
In this success story, Jan Meireleire, Engineering Manager at Ashland explains how the plant in Doel, Belgium benefits greatly from implementing TrendMiner’s self-service industrial analytics software – including solving previously unsolvable production issue, enhancing their reliability, quality and profitability, and increasing GMP production throughput.
Their Journey
Ashland consists of two commercial units: performance materials and specialty ingredients. Through the years, the plant in Belgium slowly changed their product towards use for personal care and pharmaceuticals.
New market sparks new challenges. A shift towards realizing a higher added value and a lower throughput of the product was needed, as well as maintaining a highly controlled process.
Next to that, manufacturing for the pharmaceuticals market means complying to strict regulations and control regarding product quality.
Solution & Implementation
Self-service industrial analytics proved to be the solution that could help Ashland to analyze and understand their data better and leverage it to profit from digitalization. How? Historical data is brought to AspenTech software on a dedicated server. TrendMiner’s self service analytics platform is put on top of it, which enables engineers to analyze and monitor the data.
Use Case 1
Data analysis: stabilize production by thinking outside the (data) box
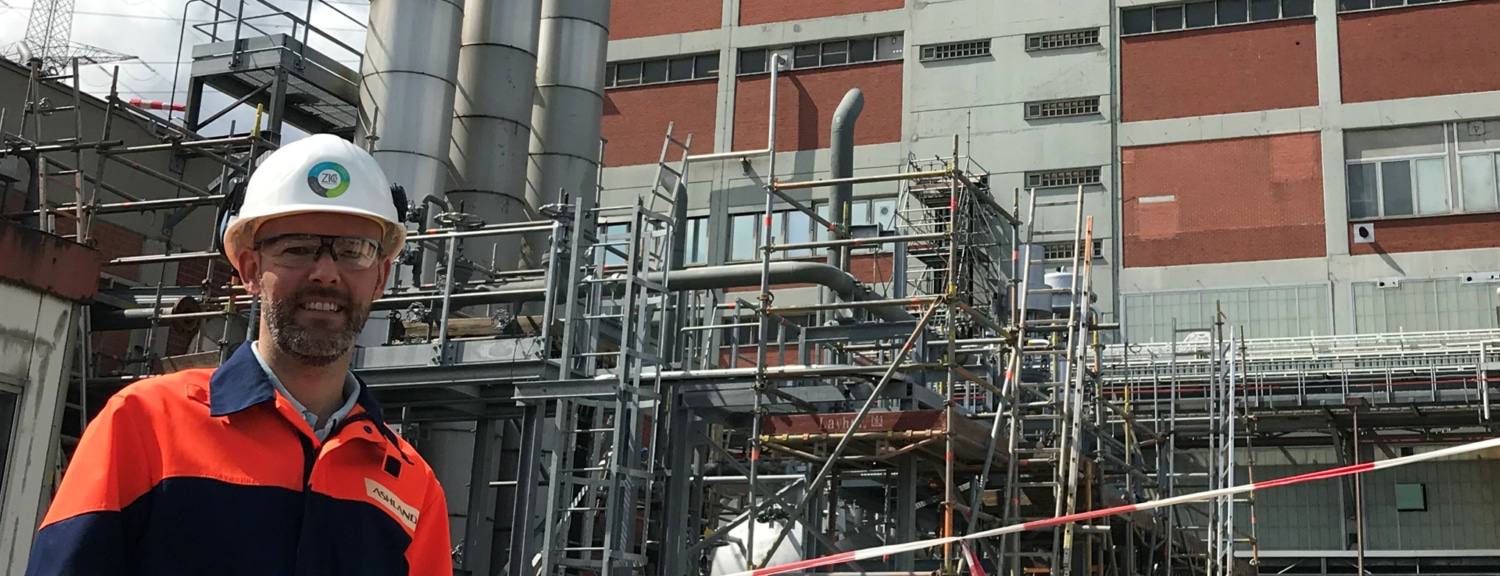
In this particular case, TrendMiner identified the most stable runs of production by filtering out data from some specific products. While all the relevant parameters in these production runs turned out to be stable, searching the entire database showed factors of influence at the very beginning of the process.
These so-called influence factors assisted with root cause analysis, helping the engineers to determine unknown correlations upstream.
With help from the software, process engineers didn’t need to extract tons of data and figures into an Excel sheet. The time that process engineers manipulate data is greatly reduced, while production is further stabilized.
Use Case 2
Data monitoring: run a smooth plant
The monitoring capabilities within TrendMiner enables process and production engineers to raise certain ‘red flags’ in time, and prevent incidents from happening in the future. Based on patterns, engineers can highlight Golden Fingerprints and are notified when an incident occurs.
At one given point in time, the process engineering group was warned about a specific event. Further analysis showed it had occurred several times the past. Instead of manually analysing data, data monitoring from TrendMiner software helped solve the incident, as well as preventing similar future ones. This is an important step towards a highly controlled process.
Benefits
Implementing TrendMiner’s self-service industrial analytics platform has helped Ashland to solve previously unsolvable production issues and enhance quality. Also, the on-target production of GMP products increased from 70% to 95%.
In this video Kobe Debie, Process Engineer at Ashland explains how TrendMiner helps to continuously improve their production process for both their continuous and batch production.
Subscribe to our newsletter
Stay up to date with our latest news and updates.
Other Webinars on demand
Explore Our Newest Content to Maximize Your Operational Efficiency
Other Resources
Explore Our Newest Content to Maximize Your Operational Efficiency