Clariant Reduces Costs and Improves Efficiency with Industrial Analytics
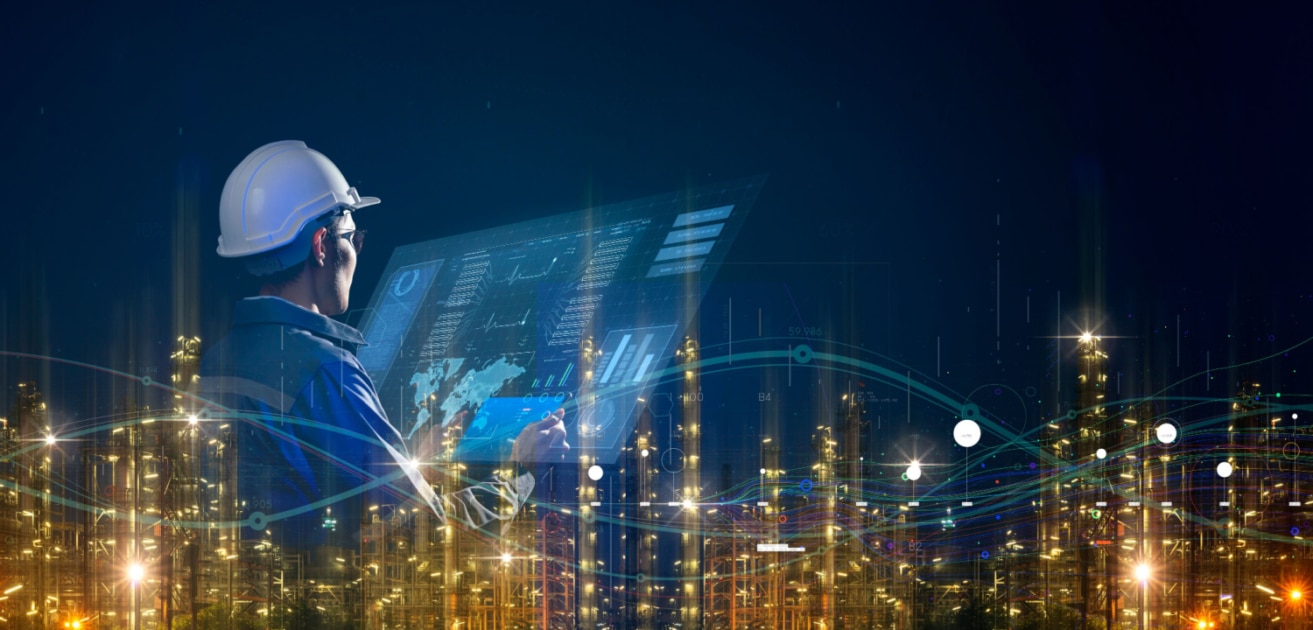
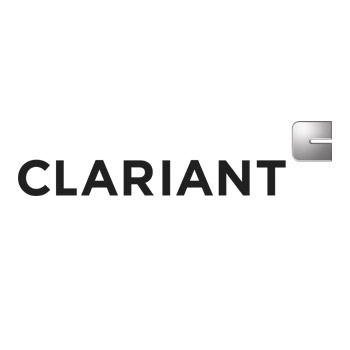
About Clariant
Clariant AG is a multinational specialty chemicals company formed in 1995 as a spin-off from Sandoz. The company is focused on four business areas: care chemicals (consumer and industrial); catalysis; natural resources (oil & gas, mining, and minerals); and plastics and coatings. Headquartered in Muttenz, Switzerland, the company operates in 53 countries. Major manufacturing sites are in Europe, North America, South America, China, and India. In 2015, sales from continuing operations were 5.9 billion Euros.
What do they say?
“Using TrendMiner, we can bring different people with different cultures, different backgrounds together and work on one project. We can view three sites on one screen in TrendMiner, which wasn’t possible before because they were in different silos. And this helps us make a stronger golden fingerprint for production. With TrendMiner, we can decrease the amount of raw material and decrease the cycle time of batches. That was the main takeaway during our trial, and what really drove people to use it afterward. They could see with their own eyes that it is faster.”
Nimet Sterneberg, Data Scientist, Clariant
Digitalization Journey & Business Challenges
Clariant began its analytics journey with five areas of focus:
- Descriptive
- Diagnostic
- Predictive
- Prescriptive
- Cognitive
During the first two phases, the company looked at how processes have behaved over time. It used TrendMiner to establish dashboards and reporting tools so that it could learn how and why process events happened.
Clariant now is in the third phase and is using the integrated Python notebooks feature to predict future behavior and develop prescriptions to change the predicted outcome as the engineers work toward a level of greater cognition.
Solution & Implementation
Clariant uses TrendMiner globally to enable data-driven analytics for its process. This empowers engineers to optimize the process across sites and allows data scientists to train models that can be consumed by the rest of the organization.
Clariant collects data at the edge of production and stores it in SAP Hana and SAP ERP solutions. Data also comes from LabVantage, which serves as the company’s laboratory information management system, and through OSIsoft PI. After storing data in a data lake and sorting it, the company uses TrendMiner to analyze time-series data from its historian. Clariant uses SAP Analytics Cloud and Microsoft Power BI for other types of analytics.
Use Cases
With the help of TrendMiner, Clariant is becoming an Augmented factory. It has begun using the software’s integrated Python notebooks feature to apply machine learning capabilities. They can use these features to extend their dashboards and set up soft sensors.
The company already has used the machine learning models to improve its DashHub view, where it created visualizations that were not originally available in the software. It also uses the capabilities to establish an even stronger golden fingerprint. Engineers can use this to create more monitors and alerts for periods when a process falls outside its normal operating parameters.
Operational experts extract data from Clariant’s historian and evaluate the time-series data in TrendMiner. They then apply proprietary algorithms and their own data science platform, create analytics on top of that, discuss the results.
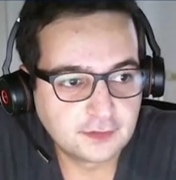
“This was the first time we were able to compare two sites, across continents and data sources in real time.”
Nimet Sterneberg, Project Leader Digitalization I Data Scientist, Clariant
Achievements
- 10% Batch cycle time reduction = 1 extra / day
- -9% Consumption by energy intensive assets
Benefits
Clariant has used TrendMiner to accelerate its digital journey from Data-driven to an Augmented Factory. TrendMiner has enabled Clariant to reduce costs by decreasing amount of raw materials used in its plants globally, which shortens batch cycle time and supports the company in reaching its 2030 energy targets. The software has also helped Clariant engineers to:
- Decrease the amount of raw material used
- Eliminate data silos within the organization
- Reduce the cycle time of batches
- See a more holistic view of operations across multiple sites
- Apply machine learning models to establish soft sensors and greater visualizations
- Predict the future behavior of its processes, and develop prescriptions to change the outcome
Success Story & Real Life Use Cases
Enriching TrendMiner Functionality with Notebooks
Watch to learn about more their company, their reasons for implementing digitalization into their operations, and to see use cases that demonstrate the value Clariant is gaining from self-service analytics.
About Clariant
Clariant AG is a multinational specialty chemicals company formed in 1995 as a spin-off from Sandoz. The company is focused on four business areas: care chemicals (consumer and industrial); catalysis; natural resources (oil & gas, mining, and minerals); and plastics and coatings. Headquartered in Muttenz, Switzerland, the company operates in 53 countries. Major manufacturing sites are in Europe, North America, South America, China, and India. In 2015, sales from continuing operations were 5.9 billion Euros.
What do they say?
“Using TrendMiner, we can bring different people with different cultures, different backgrounds together and work on one project. We can view three sites on one screen in TrendMiner, which wasn’t possible before because they were in different silos. And this helps us make a stronger golden fingerprint for production. With TrendMiner, we can decrease the amount of raw material and decrease the cycle time of batches. That was the main takeaway during our trial, and what really drove people to use it afterward. They could see with their own eyes that it is faster.”
Nimet Sterneberg, Data Scientist, Clariant
Digitalization Journey & Business Challenges
Clariant began its analytics journey with five areas of focus:
- Descriptive
- Diagnostic
- Predictive
- Prescriptive
- Cognitive
During the first two phases, the company looked at how processes have behaved over time. It used TrendMiner to establish dashboards and reporting tools so that it could learn how and why process events happened.
Clariant now is in the third phase and is using the integrated Python notebooks feature to predict future behavior and develop prescriptions to change the predicted outcome as the engineers work toward a level of greater cognition.
Solution & Implementation
Clariant uses TrendMiner globally to enable data-driven analytics for its process. This empowers engineers to optimize the process across sites and allows data scientists to train models that can be consumed by the rest of the organization.
Clariant collects data at the edge of production and stores it in SAP Hana and SAP ERP solutions. Data also comes from LabVantage, which serves as the company’s laboratory information management system, and through OSIsoft PI. After storing data in a data lake and sorting it, the company uses TrendMiner to analyze time-series data from its historian. Clariant uses SAP Analytics Cloud and Microsoft Power BI for other types of analytics.
Use Cases
With the help of TrendMiner, Clariant is becoming an Augmented factory. It has begun using the software’s integrated Python notebooks feature to apply machine learning capabilities. They can use these features to extend their dashboards and set up soft sensors.
The company already has used the machine learning models to improve its DashHub view, where it created visualizations that were not originally available in the software. It also uses the capabilities to establish an even stronger golden fingerprint. Engineers can use this to create more monitors and alerts for periods when a process falls outside its normal operating parameters.
Operational experts extract data from Clariant’s historian and evaluate the time-series data in TrendMiner. They then apply proprietary algorithms and their own data science platform, create analytics on top of that, discuss the results.
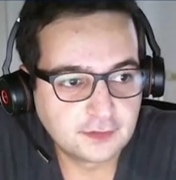
“This was the first time we were able to compare two sites, across continents and data sources in real time.”
Nimet Sterneberg, Project Leader Digitalization I Data Scientist, Clariant
Achievements
- 10% Batch cycle time reduction = 1 extra / day
- -9% Consumption by energy intensive assets
Benefits
Clariant has used TrendMiner to accelerate its digital journey from Data-driven to an Augmented Factory. TrendMiner has enabled Clariant to reduce costs by decreasing amount of raw materials used in its plants globally, which shortens batch cycle time and supports the company in reaching its 2030 energy targets. The software has also helped Clariant engineers to:
- Decrease the amount of raw material used
- Eliminate data silos within the organization
- Reduce the cycle time of batches
- See a more holistic view of operations across multiple sites
- Apply machine learning models to establish soft sensors and greater visualizations
- Predict the future behavior of its processes, and develop prescriptions to change the outcome
Success Story & Real Life Use Cases
Enriching TrendMiner Functionality with Notebooks
Watch to learn about more their company, their reasons for implementing digitalization into their operations, and to see use cases that demonstrate the value Clariant is gaining from self-service analytics.
Subscribe to our newsletter
Stay up to date with our latest news and updates.
Other Webinars on demand
Explore Our Newest Content to Maximize Your Operational Efficiency
Other Resources
Explore Our Newest Content to Maximize Your Operational Efficiency