Creating Contextual Prescriptions from the Root Cause Analysis of a Sulfur Recovery Unit
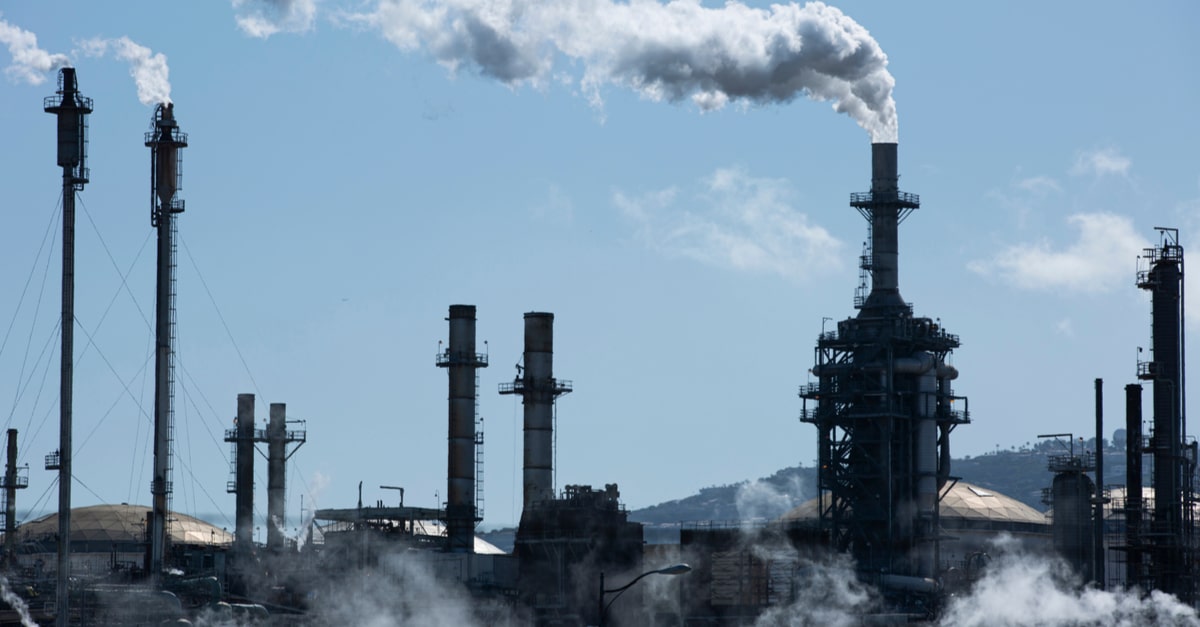
Situation
The most common way to convert H2S gas coming from petroleum during refinement is by using the Claus process. The process has multiple stages because of its chemical equilibrium. A feed gas containing a high concentration of H2S must be pre-heated using steam. The gas then enters the first converter, where it undergoes partial conversion toward pure sulfur. Part of the sulfur is removed from the gas stream before entering the second converter. In the final stage, the pure sulfur is removed and the remaining gas containing small amounts of H2S goes downstream to a treatment plant.
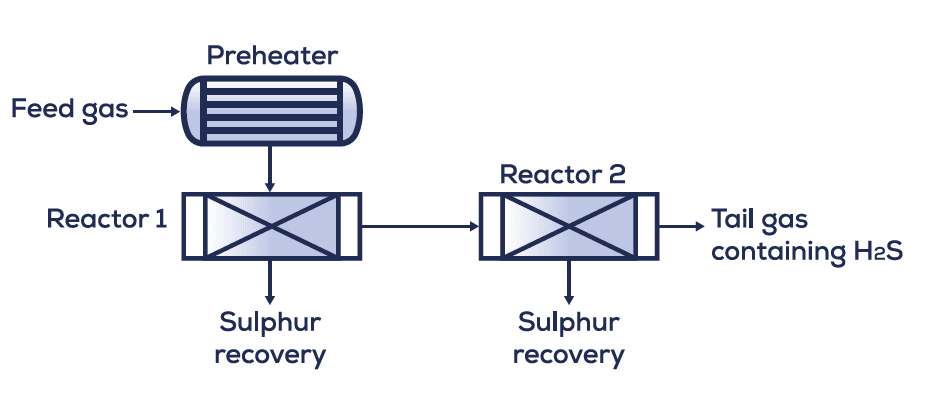
Problem
While viewing recent trends of a sulfur recovery unit on a TrendHub dashboard, engineers noticed that the amount of sulfur produced in the recovery unit, represented as tons per day, has dropped significantly. Process experts also discovered that the sulfur yield is declining, which indicates a lower conversion in the plant. As a result, the higher amount of H2S remaining in the gas stream puts too much load on the gas treatment plant. This anomaly could have environmental and regulatory consequences, so engineers want to save the results of the analysis so they can be used as a prescription for solving a similar problem in the future.
Solution
- Identify the root cause of the low sulfur recovery using TrendMiner
- Create monitors to identify anomalous periods in the data and track those periods by saving them into events
- Apply filters to the structured time-series data to create a report with contextual views
- Extend the report to add tags that note measurements of sulfur yield, H2S concentration, chemical converter parameters, and other relevant data
Challenges
Several factors could cause low sulfur recovery. Engineers might find an issue with the catalyst in the converters, temperature of the converters, temperatures of the condensers, or the control systems themselves.
Results
- Using TrendMiner, process experts determine that periods of low sulfur recovery corresponded with cooler temperatures in the converter
- Engineers discover that the root cause was a malfunctioning temperature control valve upstream from the converter
- Process experts now can create monitors to identify anomalous periods in the data and track those periods by saving them as contextual events that can be used by other engineers in the future
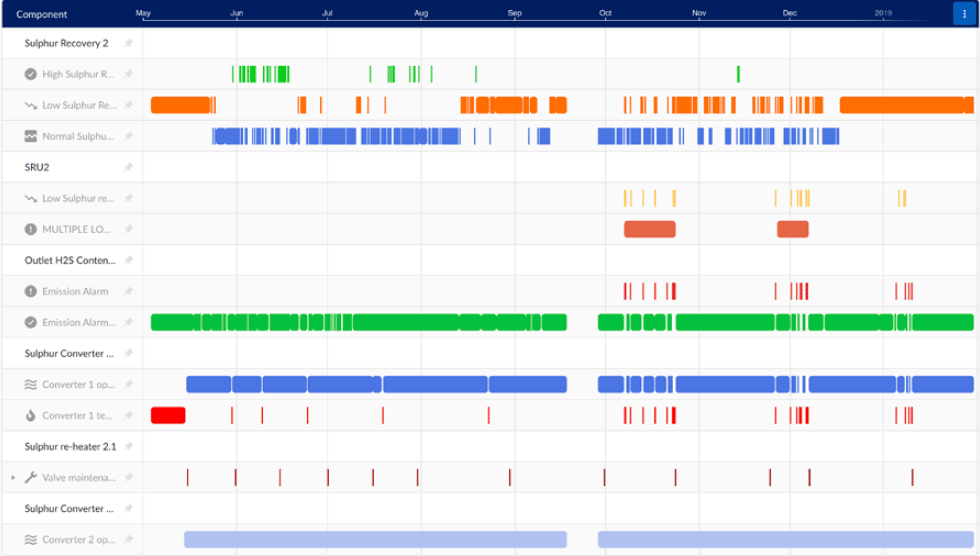
Situation
The most common way to convert H2S gas coming from petroleum during refinement is by using the Claus process. The process has multiple stages because of its chemical equilibrium. A feed gas containing a high concentration of H2S must be pre-heated using steam. The gas then enters the first converter, where it undergoes partial conversion toward pure sulfur. Part of the sulfur is removed from the gas stream before entering the second converter. In the final stage, the pure sulfur is removed and the remaining gas containing small amounts of H2S goes downstream to a treatment plant.
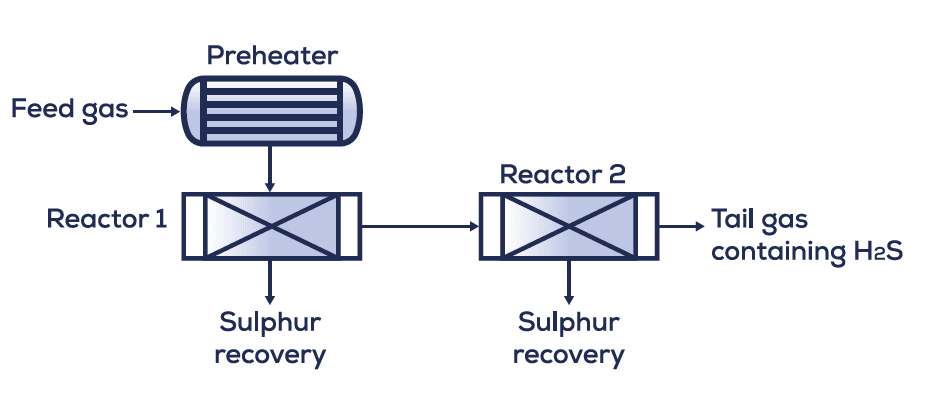
Problem
While viewing recent trends of a sulfur recovery unit on a TrendHub dashboard, engineers noticed that the amount of sulfur produced in the recovery unit, represented as tons per day, has dropped significantly. Process experts also discovered that the sulfur yield is declining, which indicates a lower conversion in the plant. As a result, the higher amount of H2S remaining in the gas stream puts too much load on the gas treatment plant. This anomaly could have environmental and regulatory consequences, so engineers want to save the results of the analysis so they can be used as a prescription for solving a similar problem in the future.
Solution
- Identify the root cause of the low sulfur recovery using TrendMiner
- Create monitors to identify anomalous periods in the data and track those periods by saving them into events
- Apply filters to the structured time-series data to create a report with contextual views
- Extend the report to add tags that note measurements of sulfur yield, H2S concentration, chemical converter parameters, and other relevant data
Challenges
Several factors could cause low sulfur recovery. Engineers might find an issue with the catalyst in the converters, temperature of the converters, temperatures of the condensers, or the control systems themselves.
Results
- Using TrendMiner, process experts determine that periods of low sulfur recovery corresponded with cooler temperatures in the converter
- Engineers discover that the root cause was a malfunctioning temperature control valve upstream from the converter
- Process experts now can create monitors to identify anomalous periods in the data and track those periods by saving them as contextual events that can be used by other engineers in the future
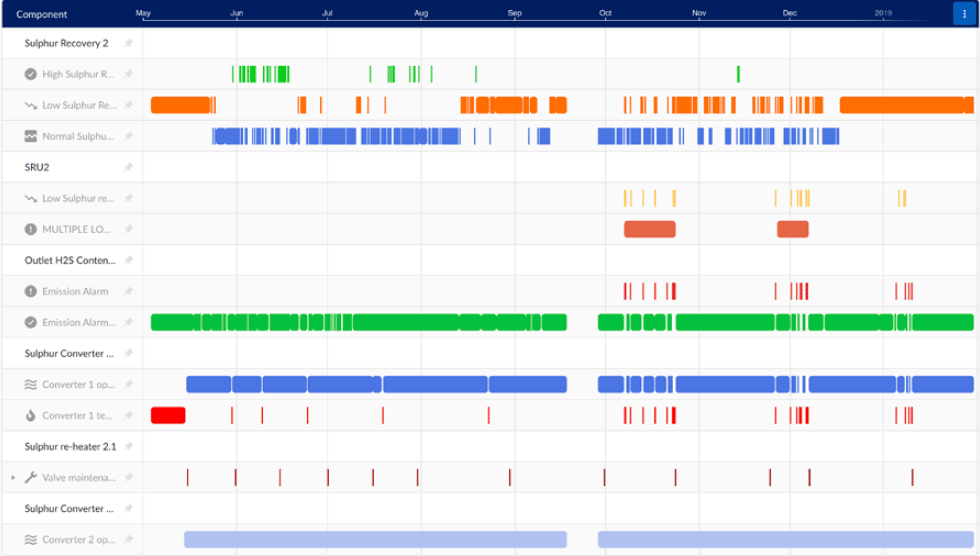
Subscribe to our newsletter
Stay up to date with our latest news and updates.
Other Webinars on demand
Explore Our Newest Content to Maximize Your Operational Efficiency
Other Resources
Explore Our Newest Content to Maximize Your Operational Efficiency