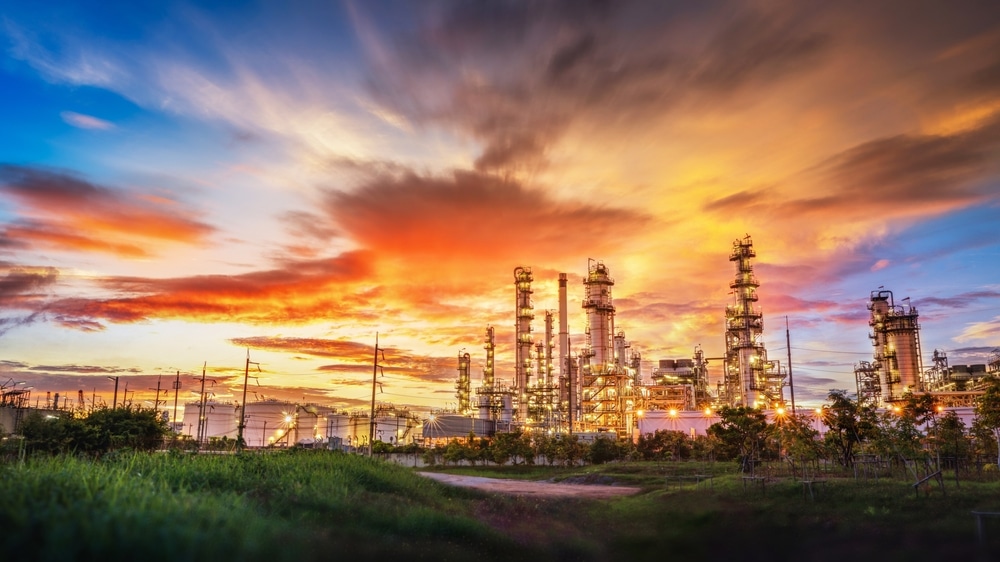
Situation
This European chemical plant produces 17 bar steam in an aftercooler. The steam is consumed at various points on the production lines. The plant includes multiple chambers for production. As a rule, the production of 17 bar steam in these chambers is not sufficient to cover the total demand. Even if the chambers are operating simultaneously, additional steam must be imported from the network. The demand for 17 bar increases abruptly to keep the chambers in a start-up condition if one or both chambers is out of service.
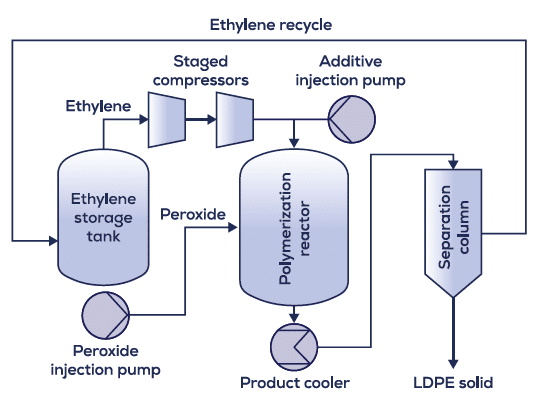
Problem
Engineers wanted to know when 17 bar steam consumption exceeded production in the aftercooler. However, they did not have a method to determine the normal steam consumption so they would know when consumption deviated from expectations. Process experts had been using spreadsheets to determine when 17 bar steam consumption might increase, but they could not create models using this method. Knowing when steam consumption was excessive would allow process experts to intervene in time to prevent a possible shutdown.
Solution
Engineers decided to create linear energy models that could be used to set up soft sensors to monitor for periods when 17 bar steam consumption was excessive. Engineers could use those soft sensors to design alerts that would notify key stakeholders of the excessive consumption.
Approach
- Calculate steam balance as a new formula summarizing the average steam consumption.
- Prepare and clean data for analysis.
- Identify normal steam consumption.
- Create soft sensors to monitor for consumption deviations.
- Set up email alerts to key stakeholders when consumption does not match the model.
Results
- Engineers could see when 17 bar steam consumption was excessive.
- Using TrendMiner, process experts were able to build the model quickly and easily and iterate findings until they could find a permanent solution.
- The software designed sub-models with high predictive power that also identified local weaknesses in the data.
- When excessive 17 bar steam consumption occurred, TrendMiner sent notifications to process experts that allowed them to intervene in time.
Situation
This European chemical plant produces 17 bar steam in an aftercooler. The steam is consumed at various points on the production lines. The plant includes multiple chambers for production. As a rule, the production of 17 bar steam in these chambers is not sufficient to cover the total demand. Even if the chambers are operating simultaneously, additional steam must be imported from the network. The demand for 17 bar increases abruptly to keep the chambers in a start-up condition if one or both chambers is out of service.
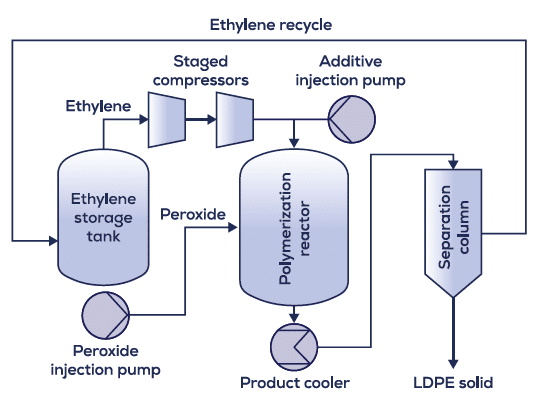
Problem
Engineers wanted to know when 17 bar steam consumption exceeded production in the aftercooler. However, they did not have a method to determine the normal steam consumption so they would know when consumption deviated from expectations. Process experts had been using spreadsheets to determine when 17 bar steam consumption might increase, but they could not create models using this method. Knowing when steam consumption was excessive would allow process experts to intervene in time to prevent a possible shutdown.
Solution
Engineers decided to create linear energy models that could be used to set up soft sensors to monitor for periods when 17 bar steam consumption was excessive. Engineers could use those soft sensors to design alerts that would notify key stakeholders of the excessive consumption.
Approach
- Calculate steam balance as a new formula summarizing the average steam consumption.
- Prepare and clean data for analysis.
- Identify normal steam consumption.
- Create soft sensors to monitor for consumption deviations.
- Set up email alerts to key stakeholders when consumption does not match the model.
Results
- Engineers could see when 17 bar steam consumption was excessive.
- Using TrendMiner, process experts were able to build the model quickly and easily and iterate findings until they could find a permanent solution.
- The software designed sub-models with high predictive power that also identified local weaknesses in the data.
- When excessive 17 bar steam consumption occurred, TrendMiner sent notifications to process experts that allowed them to intervene in time.
Subscribe to our newsletter
Stay up to date with our latest news and updates.
Other Webinars on demand
Explore Our Newest Content to Maximize Your Operational Efficiency
Other Resources
Explore Our Newest Content to Maximize Your Operational Efficiency