Life Monitoring & Prediction of Useful Catalyst Life for Predictive Maintenance
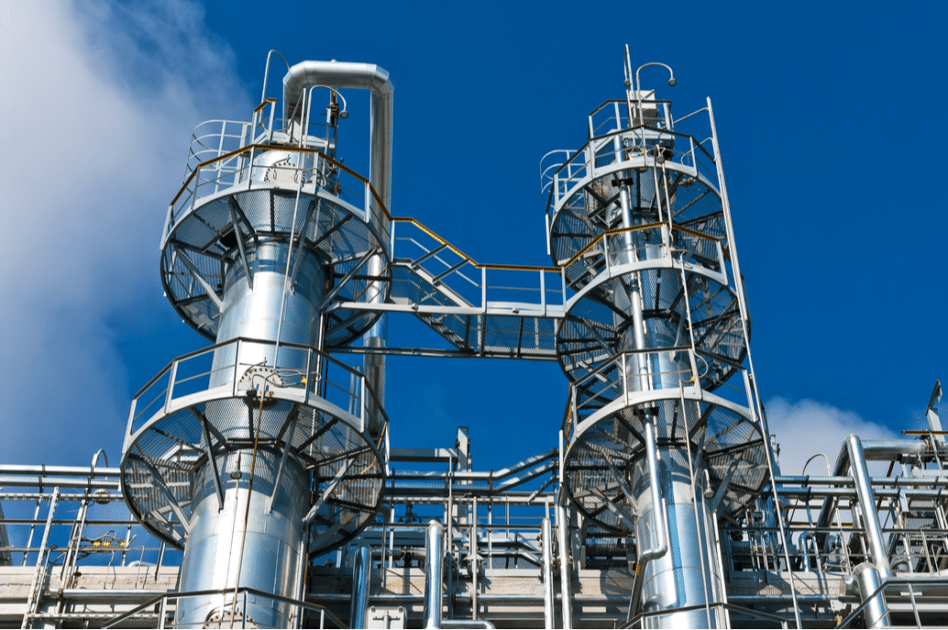
Situation
In certain chemical plants, reactors may contain catalyst beds. The catalyst bed loses activity over time and needs to be replaced on a routine basis. It is critical that preventative maintenance is scheduled at least a few weeks prior to catalyst failure, as any premature catalyst failure could be detrimental to the production lines.
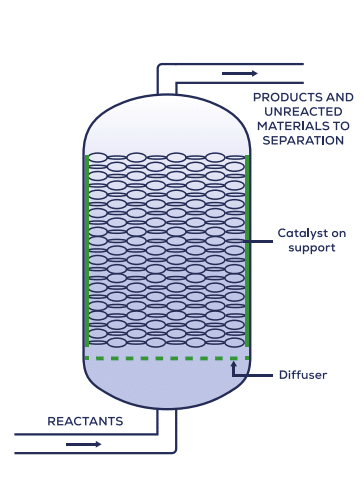
Problem
Due to variability in catalyst life, forecasting when the catalyst will fail can be challenging. As supply chain, maintenance, and operations would all be affected in the event of a premature catalyst failure, it is critical to replace the catalyst prior to failure. Traditionally, there has been no easy way to predict when a catalyst bed would fail.
Solution
The engineers wanted to monitor the failure rate of the zinc oxide catalyst, so they can forecast when the catalyst will reach the end of useful life. Knowing this in time helps to schedule maintenance timely.
Approach
- Smoothed out reactor temperature tags using TrendMiner aggregations.
- Zoomed in to the current catalyst run temperature and utilized predictive mode with two historical layers.
- Visually identified the end of useful catalyst life on the sub-layers.
- Placed scooters for the two most similar catalyst runs to quantitatively mark the threshold for the end of useful life
Results
- With the click of a button, a forecast based on historical data can be presented to the subject matter expert, who can then inform maintenance, operations, and supply chain to allow for more accurate production scheduling.
- The useful remaining catalyst life, based on historical performance, can be successfully predicted, which in this case was 3-7 months.
- The analyses performed can be applied to other packed bed reactors.
Situation
In certain chemical plants, reactors may contain catalyst beds. The catalyst bed loses activity over time and needs to be replaced on a routine basis. It is critical that preventative maintenance is scheduled at least a few weeks prior to catalyst failure, as any premature catalyst failure could be detrimental to the production lines.
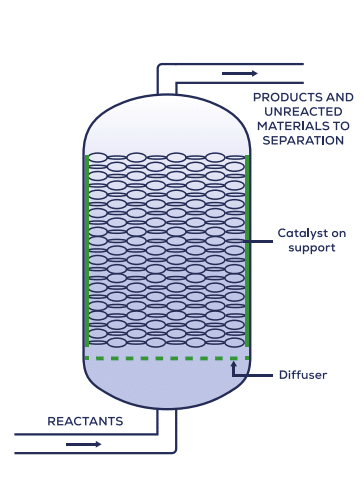
Problem
Due to variability in catalyst life, forecasting when the catalyst will fail can be challenging. As supply chain, maintenance, and operations would all be affected in the event of a premature catalyst failure, it is critical to replace the catalyst prior to failure. Traditionally, there has been no easy way to predict when a catalyst bed would fail.
Solution
The engineers wanted to monitor the failure rate of the zinc oxide catalyst, so they can forecast when the catalyst will reach the end of useful life. Knowing this in time helps to schedule maintenance timely.
Approach
- Smoothed out reactor temperature tags using TrendMiner aggregations.
- Zoomed in to the current catalyst run temperature and utilized predictive mode with two historical layers.
- Visually identified the end of useful catalyst life on the sub-layers.
- Placed scooters for the two most similar catalyst runs to quantitatively mark the threshold for the end of useful life
Results
- With the click of a button, a forecast based on historical data can be presented to the subject matter expert, who can then inform maintenance, operations, and supply chain to allow for more accurate production scheduling.
- The useful remaining catalyst life, based on historical performance, can be successfully predicted, which in this case was 3-7 months.
- The analyses performed can be applied to other packed bed reactors.
Download now
Subscribe to our newsletter
Stay up to date with our latest news and updates.
Other Webinars on Demand
Press Play on Operational Improvement
Other Resources
Explore Our Newest Content to Maximize Your Operational Efficiency