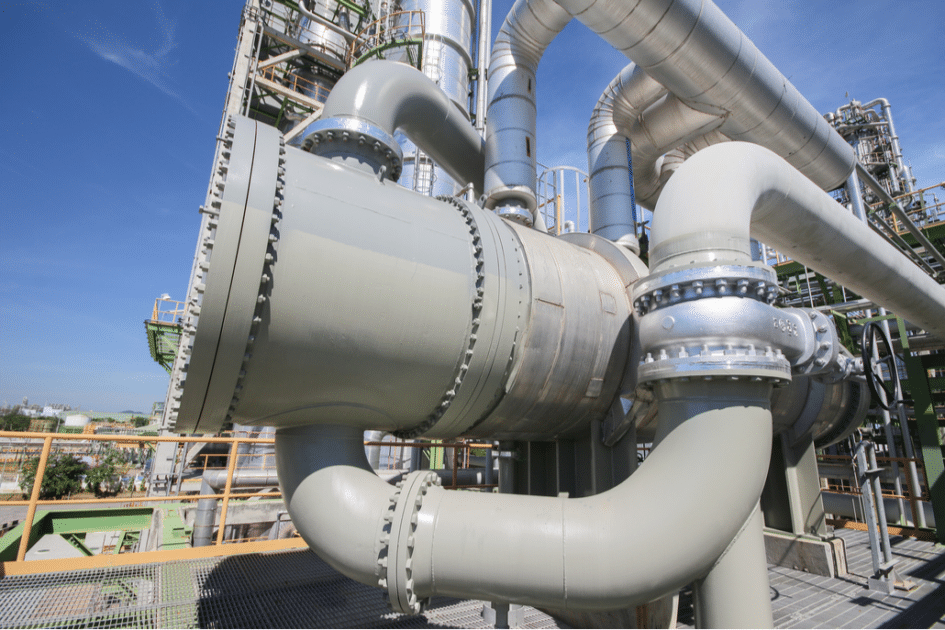
Situation
At this specialty and commodity chemicals plant, production is a continuous process. Among the critical equipment on site is a shell and tube heat exchanger. At the plant, process gas from that heat exchanger goes to a baghouse that has a maximum upper-temperature limit. Based on process variables, the cooled process gas entering the baghouse has an arbitrary set upper limit of a temperature ~10° lower than the actual maximum upper-temperature limit. The plant wanted to raise the upper limit of the temperature after the turn-around.
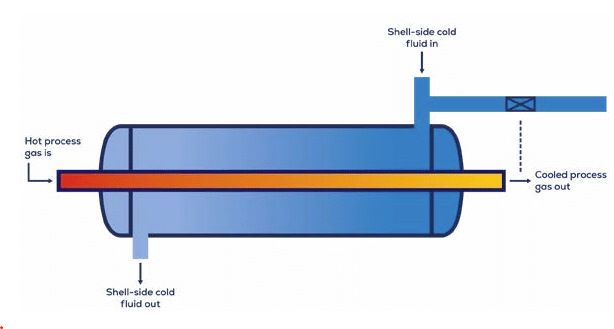
Problem
In the past, the plant operated above the arbitrary set upper limit and wanted to compare the conditions of those time intervals to the current operation. One obstacle was that the shell-side inlet flow was not controlled. Instead, a bypass was used to gauge flow based on the outlet tube-side fluid temperature going to the baghouse.
Solution
The engineers wanted to find time periods and process parameters when the tube-side outlet temperature operated above the current arbitrary set upper limit. This was to be used as a reference when trying to increase the temperature limit of the tube-side outlet to the baghouse.
Challenges
- Searching through years of data to find condition(s) when the tube-side outlet temperature operated above the arbitrary set upper limit (descriptive statistics)
- Comparing all the process parameters with the current conditions.
- Validating if raising the arbitrary set upper limit temperature was feasible
Approach
- TrendMiner was used to perform a value based search (VBS) on
the baghouse inlet temperature between two higher temperatures. - The engineers were able to layer the search results and perform another VBS with the baghouse inlet temperature between two lower temperatures.
- The engineers could then layer these results on top of the first search results and compare the two sets of operating conditions.
Results
The process engineer was able to validate all the calculations. The historical process parameters validated the engineer’s calculations and provided proof to the safety & environmental team. The use case led to an operational optimization, resulting in:
• Cost reduction
• Time savings
• Higher energy efficiency of the heat exchanger
Situation
At this specialty and commodity chemicals plant, production is a continuous process. Among the critical equipment on site is a shell and tube heat exchanger. At the plant, process gas from that heat exchanger goes to a baghouse that has a maximum upper-temperature limit. Based on process variables, the cooled process gas entering the baghouse has an arbitrary set upper limit of a temperature ~10° lower than the actual maximum upper-temperature limit. The plant wanted to raise the upper limit of the temperature after the turn-around.
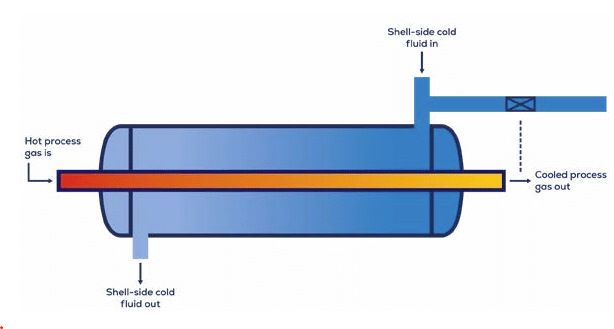
Problem
In the past, the plant operated above the arbitrary set upper limit and wanted to compare the conditions of those time intervals to the current operation. One obstacle was that the shell-side inlet flow was not controlled. Instead, a bypass was used to gauge flow based on the outlet tube-side fluid temperature going to the baghouse.
Solution
The engineers wanted to find time periods and process parameters when the tube-side outlet temperature operated above the current arbitrary set upper limit. This was to be used as a reference when trying to increase the temperature limit of the tube-side outlet to the baghouse.
Challenges
- Searching through years of data to find condition(s) when the tube-side outlet temperature operated above the arbitrary set upper limit (descriptive statistics)
- Comparing all the process parameters with the current conditions.
- Validating if raising the arbitrary set upper limit temperature was feasible
Approach
- TrendMiner was used to perform a value based search (VBS) on
the baghouse inlet temperature between two higher temperatures. - The engineers were able to layer the search results and perform another VBS with the baghouse inlet temperature between two lower temperatures.
- The engineers could then layer these results on top of the first search results and compare the two sets of operating conditions.
Results
The process engineer was able to validate all the calculations. The historical process parameters validated the engineer’s calculations and provided proof to the safety & environmental team. The use case led to an operational optimization, resulting in:
• Cost reduction
• Time savings
• Higher energy efficiency of the heat exchanger
Subscribe to our newsletter
Stay up to date with our latest news and updates.
Other Webinars on demand
Explore Our Newest Content to Maximize Your Operational Efficiency
Other Resources
Explore Our Newest Content to Maximize Your Operational Efficiency