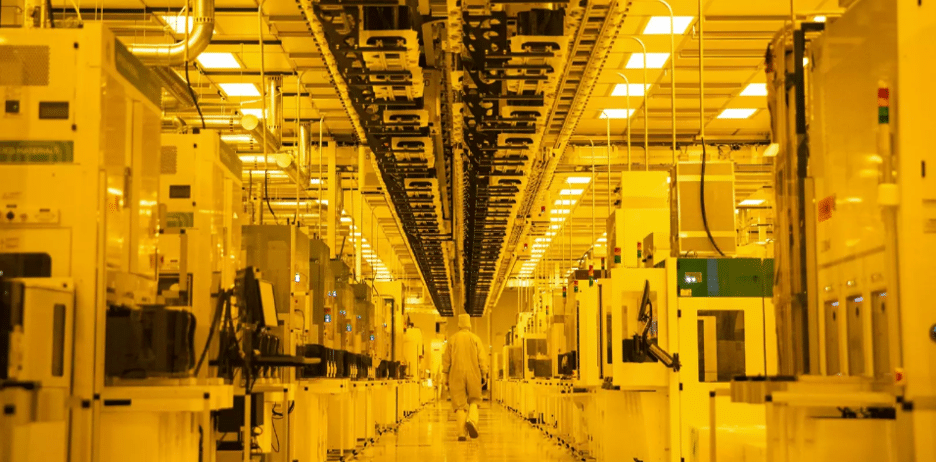
Situation
In the High-Tech Manufacturing industry, maintaining ultra-clean environments is essential due to the sensitivity of electronic components to contamination. Ultra-Pure Air (UPA) systems are critical in ensuring that the air quality meets stringent requirements, thus protecting the integrity of the manufacturing process for high-value products, such as semiconductors. These systems used in cleanrooms utilize compressors, dryers, and various air filters to provide the necessary clean, dry air. Given the high energy consumption associated with UPA systems, optimizing their efficiency is crucial to reducing operating costs. Moreover, UPA systems ensure reliable production.
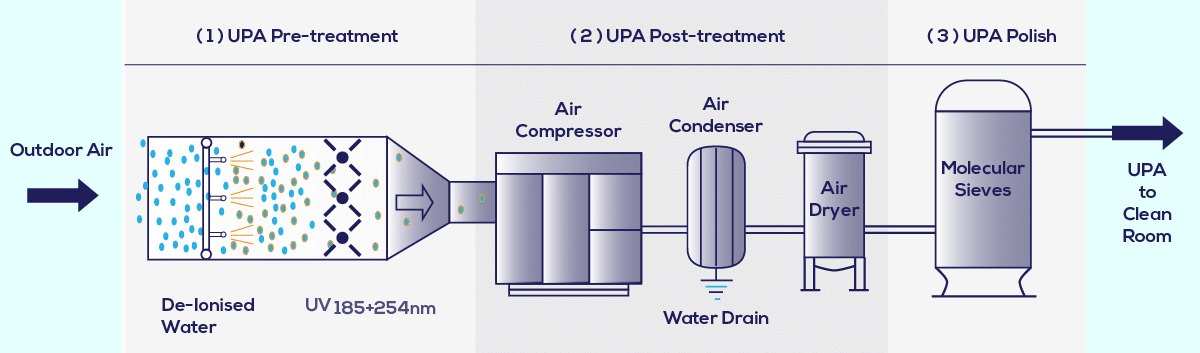
Problem
A customer experienced air losses in their UPA system for semiconductor production. Undetected air losses lead to inefficiencies, increased energy consumption, and higher operating costs; therefore, they must be identified. Calculating the air loss across the entire UPA system can inform engineers where they are losing efficiency and how much opportunity there is for improvement.
Challenges
- Data Overload: Engineers had to manage and analyze large volumes of process data to identify air losses, which can be overwhelming without the right tools at hand.
- Cumbersome analysis with non-purpose-built tools: Comparing data year-over-year to track performance and identify trends was time-consuming when engineers were using Excel.
- Collaboration barriers: Engineers could not share insights about air losses with colleagues or other departments within the facility.
Solution
- With TrendMiner, engineers could calculate the air loss for each compressor and the entire UPA system within minutes.
- Easy and fast time navigation and layering allowed for quick comparison of different time periods.
- Engineers calculated the total air loss for one facility during the whole year in a few clicks.
- They set up monitors to get alerted when air losses occurred and created a dashboard that provided a holistic overview of all air losses in the facility.
Results
- Enhanced Visibility – TrendMiner helps to provide clear, actionable insights into where air losses are occurring, facilitating prompt corrective actions.
- Self-Service Analysis – Empowers everyone to set up analyses in just a few clicks.
- Improved Efficiency – Streamlines data analysis and reporting, freeing up engineering resources to focus on other critical tasks.
- Knowledge Sharing – Comprehensive dashboards allow engineers to share their insights with colleagues.
- Cost Savings – By identifying and reducing air losses, engineers identified a loss of over $100k due to air losses in the last year in one facility.
- Scalability – The solution can be scaled to other departments, production lines, or facilities, ensuring consistent efficiency improvements across the organization.
Identifying air loss helps improve the performance, cost-effectiveness, reliability, and environmental sustainability of semiconductor manufacturing operations.
Situation
In the High-Tech Manufacturing industry, maintaining ultra-clean environments is essential due to the sensitivity of electronic components to contamination. Ultra-Pure Air (UPA) systems are critical in ensuring that the air quality meets stringent requirements, thus protecting the integrity of the manufacturing process for high-value products, such as semiconductors. These systems used in cleanrooms utilize compressors, dryers, and various air filters to provide the necessary clean, dry air. Given the high energy consumption associated with UPA systems, optimizing their efficiency is crucial to reducing operating costs. Moreover, UPA systems ensure reliable production.
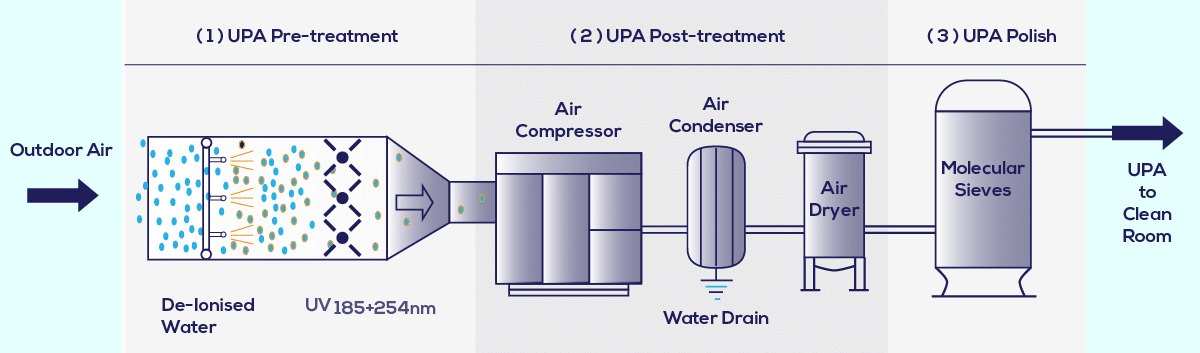
Problem
A customer experienced air losses in their UPA system for semiconductor production. Undetected air losses lead to inefficiencies, increased energy consumption, and higher operating costs; therefore, they must be identified. Calculating the air loss across the entire UPA system can inform engineers where they are losing efficiency and how much opportunity there is for improvement.
Challenges
- Data Overload: Engineers had to manage and analyze large volumes of process data to identify air losses, which can be overwhelming without the right tools at hand.
- Cumbersome analysis with non-purpose-built tools: Comparing data year-over-year to track performance and identify trends was time-consuming when engineers were using Excel.
- Collaboration barriers: Engineers could not share insights about air losses with colleagues or other departments within the facility.
Solution
- With TrendMiner, engineers could calculate the air loss for each compressor and the entire UPA system within minutes.
- Easy and fast time navigation and layering allowed for quick comparison of different time periods.
- Engineers calculated the total air loss for one facility during the whole year in a few clicks.
- They set up monitors to get alerted when air losses occurred and created a dashboard that provided a holistic overview of all air losses in the facility.
Results
- Enhanced Visibility – TrendMiner helps to provide clear, actionable insights into where air losses are occurring, facilitating prompt corrective actions.
- Self-Service Analysis – Empowers everyone to set up analyses in just a few clicks.
- Improved Efficiency – Streamlines data analysis and reporting, freeing up engineering resources to focus on other critical tasks.
- Knowledge Sharing – Comprehensive dashboards allow engineers to share their insights with colleagues.
- Cost Savings – By identifying and reducing air losses, engineers identified a loss of over $100k due to air losses in the last year in one facility.
- Scalability – The solution can be scaled to other departments, production lines, or facilities, ensuring consistent efficiency improvements across the organization.
Identifying air loss helps improve the performance, cost-effectiveness, reliability, and environmental sustainability of semiconductor manufacturing operations.
Download now
Subscribe to our newsletter
Stay up to date with our latest news and updates.
Other Webinars on demand
Explore Our Newest Content to Maximize Your Operational Efficiency
Other Resources
Explore Our Newest Content to Maximize Your Operational Efficiency