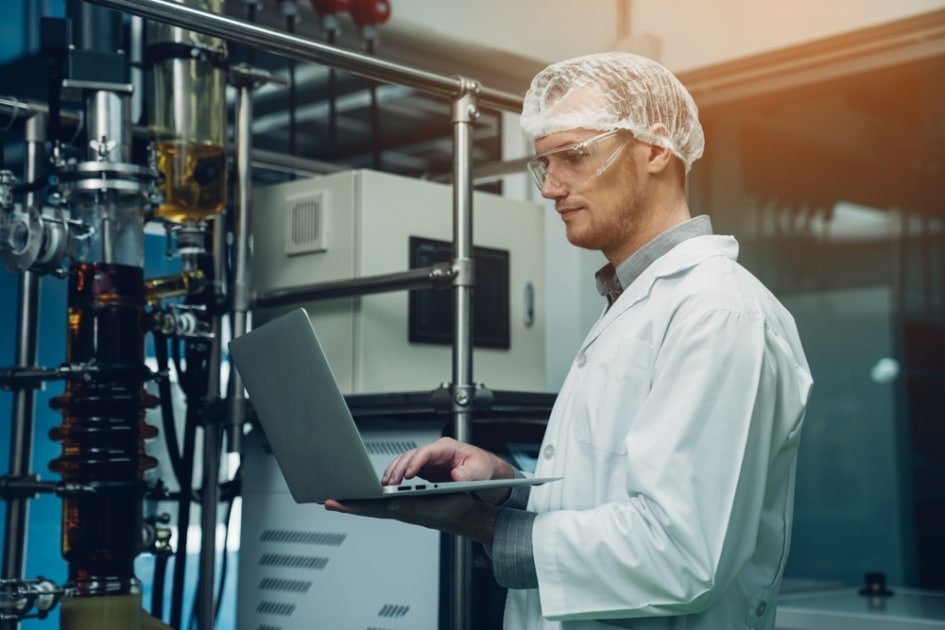
Situation
The production of dairy products is heavily regulated and requires a meticulous handling of raw material and final product. Clean-in-Place (CIP) occurs between each production batch. It helps avoid cross-contamination, ensures a quality product that meets specification, and complies with corporate and government safety regulations. In the sterilization process of a filling unit, the unit needs to heat up to 90-degrees Celsius and maintain that temperature to initiate cleaning. When the cycle time of this process step takes too long, it means that the unit did not heat to the correct temperature and the vessels in the unit have not been cleaned correctly.
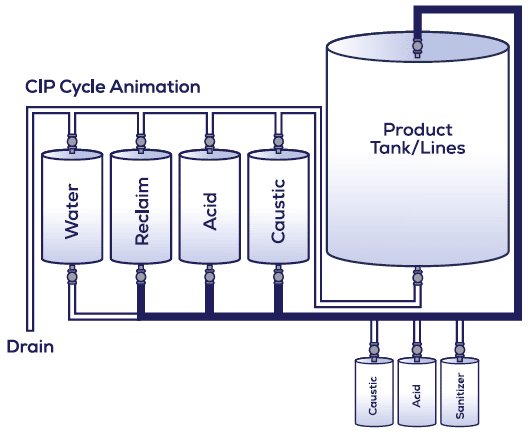
Problem
Engineers noticed that their CIP unit was not reaching the desired temperature. When it failed to clean properly, they had to run the cycle again to ensure that the vessels reached an acceptable level of sterilization. This led to costly interruptions in production and greater use of ultra-pure water used in the process.
Goals
- Ensure all CIPs are adequately triggered to avoid incomplete cleaning of production vessels
- Reduce downtime and water use by avoiding CIP anomalies
Challenges
- To better understand CIP performance, engineers first had to determine which phase is prolonging the process
Approach
- Perform various value-based searches to find the typical run time for all CIPs on a particular asset
- Set up monitors to alert operators when a CIP takes longer than expected
- Compare “failed” CIPs to determine where in which phase the anomalies were occurring
- Perform a correlation analysis to find the root cause for a decrease in vessel temperature during that CIP phase
Results
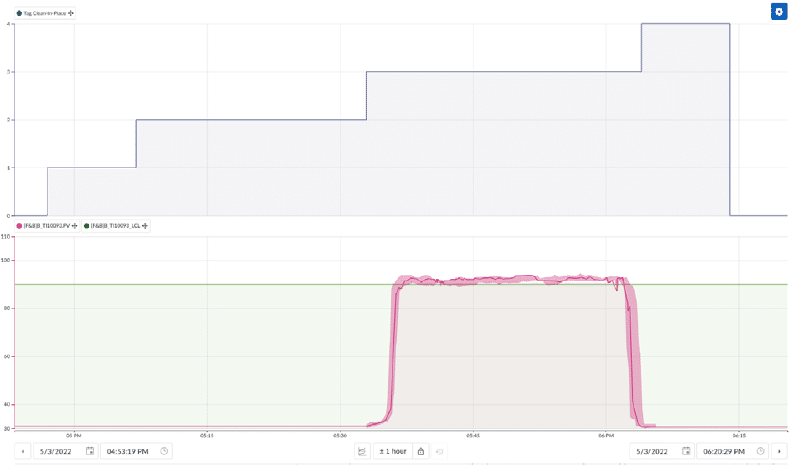
- Using TrendMiner, engineers were able to extend the water wash phase to create longer CIPs
- They also learned that an increase in steam consumption in the spray dryer caused the temperature to drop during a caustic wash
- With the CIP functioning as expected, engineers were able to reduce water usage by 60% during extended CIPs
- Established monitors will give engineers better situational awareness of the CIP unit
Situation
The production of dairy products is heavily regulated and requires a meticulous handling of raw material and final product. Clean-in-Place (CIP) occurs between each production batch. It helps avoid cross-contamination, ensures a quality product that meets specification, and complies with corporate and government safety regulations. In the sterilization process of a filling unit, the unit needs to heat up to 90-degrees Celsius and maintain that temperature to initiate cleaning. When the cycle time of this process step takes too long, it means that the unit did not heat to the correct temperature and the vessels in the unit have not been cleaned correctly.
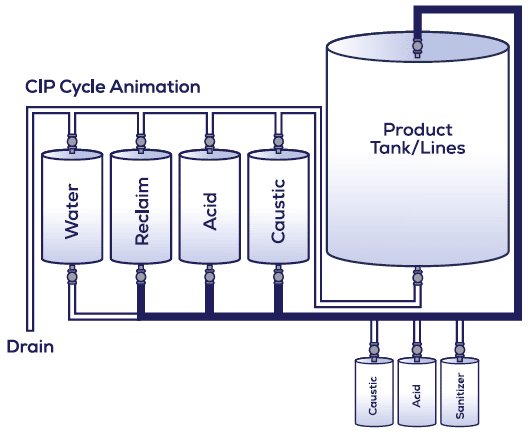
Problem
Engineers noticed that their CIP unit was not reaching the desired temperature. When it failed to clean properly, they had to run the cycle again to ensure that the vessels reached an acceptable level of sterilization. This led to costly interruptions in production and greater use of ultra-pure water used in the process.
Goals
- Ensure all CIPs are adequately triggered to avoid incomplete cleaning of production vessels
- Reduce downtime and water use by avoiding CIP anomalies
Challenges
- To better understand CIP performance, engineers first had to determine which phase is prolonging the process
Approach
- Perform various value-based searches to find the typical run time for all CIPs on a particular asset
- Set up monitors to alert operators when a CIP takes longer than expected
- Compare “failed” CIPs to determine where in which phase the anomalies were occurring
- Perform a correlation analysis to find the root cause for a decrease in vessel temperature during that CIP phase
Results
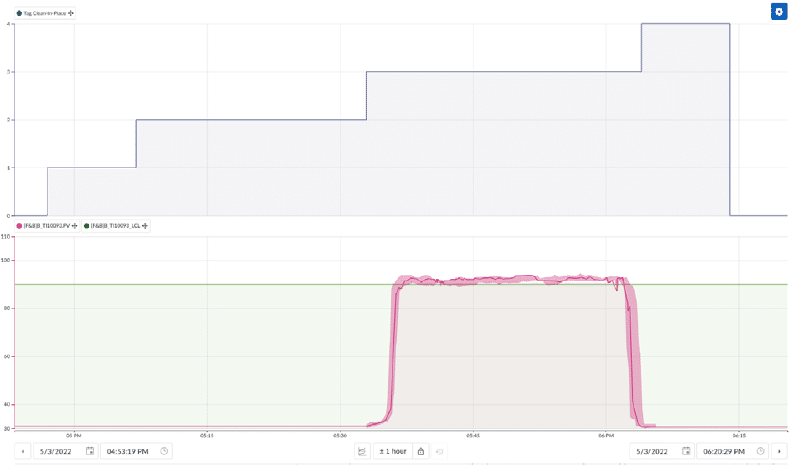
- Using TrendMiner, engineers were able to extend the water wash phase to create longer CIPs
- They also learned that an increase in steam consumption in the spray dryer caused the temperature to drop during a caustic wash
- With the CIP functioning as expected, engineers were able to reduce water usage by 60% during extended CIPs
- Established monitors will give engineers better situational awareness of the CIP unit
Download now
Subscribe to our newsletter
Stay up to date with our latest news and updates.
Other Webinars on demand
Explore Our Newest Content to Maximize Your Operational Efficiency
Other Resources
Explore Our Newest Content to Maximize Your Operational Efficiency