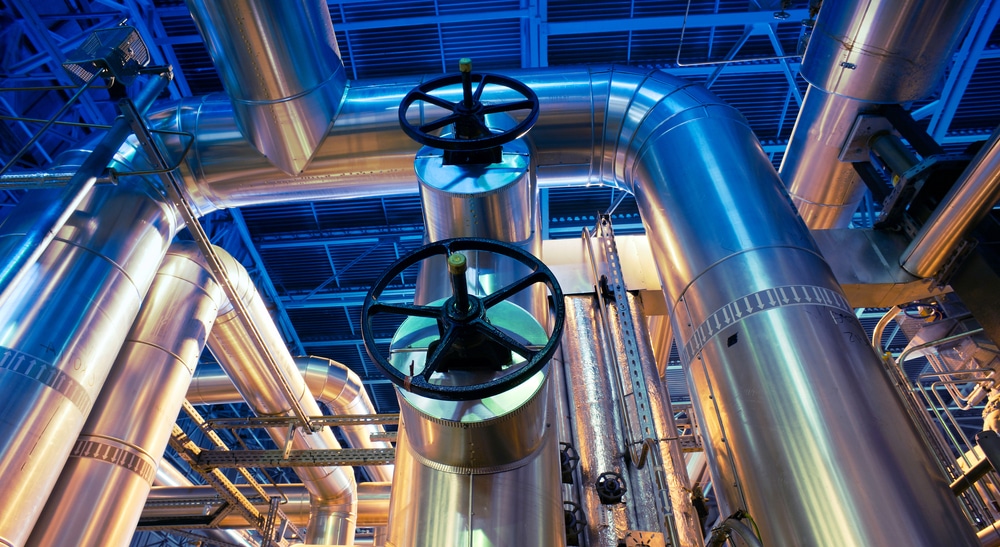
Situation
Low density polyethylene (LDPE) is produced continuously in tubular reactor under high pressure conditions at this European polyethylene plant. To keep the rate continuous, the goal is to reach constantly high throughput and operate the process under secure conditions. After the reactor has been shut down because of cleaning, it is restarted under safe conditions. Ideally, this start-up is performed as fast as possible to avoid downtime.
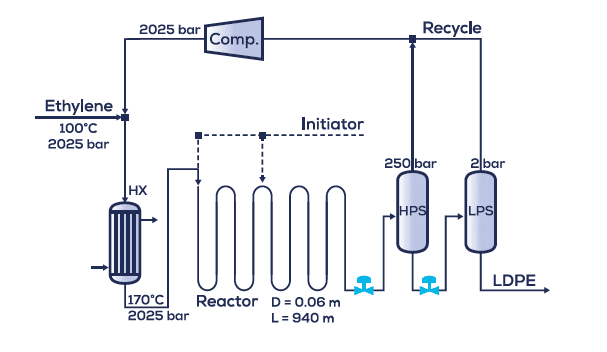
Problem
During start-up of the LDPE plant, engineers observed an unexpected, sharp, 240-bar drop in the high-pressure circuit. The pressure drop resulted in an emergency shutdown. Process experts began troubleshooting as part of the emergency shutdown procedure. Engineers wanted to find the root cause of the pressure drop on startup under stable and safe conditions and avoid additional downtime caused by mandatory emergency procedures.
Solution
- Perform an analysis in TrendMiner on influence factors, and identify correlating tags as potential root causes
- Evaluate potential candidates—such as temperatures, pressures, valve positions, and others by process engineers in process context—with high correlations to the shutdown
- Generate a hypothesis based on the influence factors with high correlations to the event, and test the hypothesis
Challenges
- The plant has procedures for troubleshooting during an emergency shutdown. However, these procedures do not cover all processes and do not provide good root cause analysis.
- Previous experience with analyzing trends includes a historian trend client and spreadsheets
Results
- After evaluating the possible influence factors in TrendMiner, process experts discovered a valve had been opened manually, but the valve was not supposed to be opened during start up
- The correlation analysis also revealed influence factors that are not checked in standard emergency troubleshooting procedure
- Engineers have immediate access to root cause analysis if the problem happens again, which can save hundreds of thousands in lost production time
Situation
Low density polyethylene (LDPE) is produced continuously in tubular reactor under high pressure conditions at this European polyethylene plant. To keep the rate continuous, the goal is to reach constantly high throughput and operate the process under secure conditions. After the reactor has been shut down because of cleaning, it is restarted under safe conditions. Ideally, this start-up is performed as fast as possible to avoid downtime.
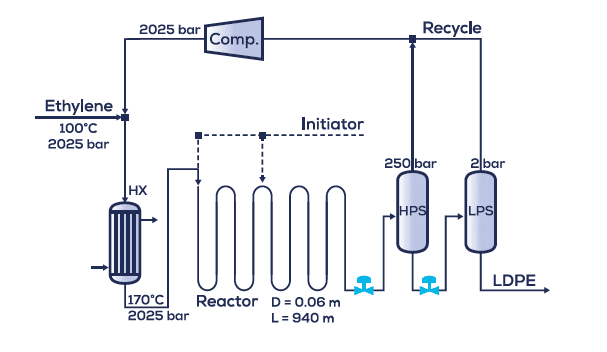
Problem
During start-up of the LDPE plant, engineers observed an unexpected, sharp, 240-bar drop in the high-pressure circuit. The pressure drop resulted in an emergency shutdown. Process experts began troubleshooting as part of the emergency shutdown procedure. Engineers wanted to find the root cause of the pressure drop on startup under stable and safe conditions and avoid additional downtime caused by mandatory emergency procedures.
Solution
- Perform an analysis in TrendMiner on influence factors, and identify correlating tags as potential root causes
- Evaluate potential candidates—such as temperatures, pressures, valve positions, and others by process engineers in process context—with high correlations to the shutdown
- Generate a hypothesis based on the influence factors with high correlations to the event, and test the hypothesis
Challenges
- The plant has procedures for troubleshooting during an emergency shutdown. However, these procedures do not cover all processes and do not provide good root cause analysis.
- Previous experience with analyzing trends includes a historian trend client and spreadsheets
Results
- After evaluating the possible influence factors in TrendMiner, process experts discovered a valve had been opened manually, but the valve was not supposed to be opened during start up
- The correlation analysis also revealed influence factors that are not checked in standard emergency troubleshooting procedure
- Engineers have immediate access to root cause analysis if the problem happens again, which can save hundreds of thousands in lost production time
Download now
Subscribe to our newsletter
Stay up to date with our latest news and updates.
Other Webinars on demand
Explore Our Newest Content to Maximize Your Operational Efficiency
Other Resources
Explore Our Newest Content to Maximize Your Operational Efficiency