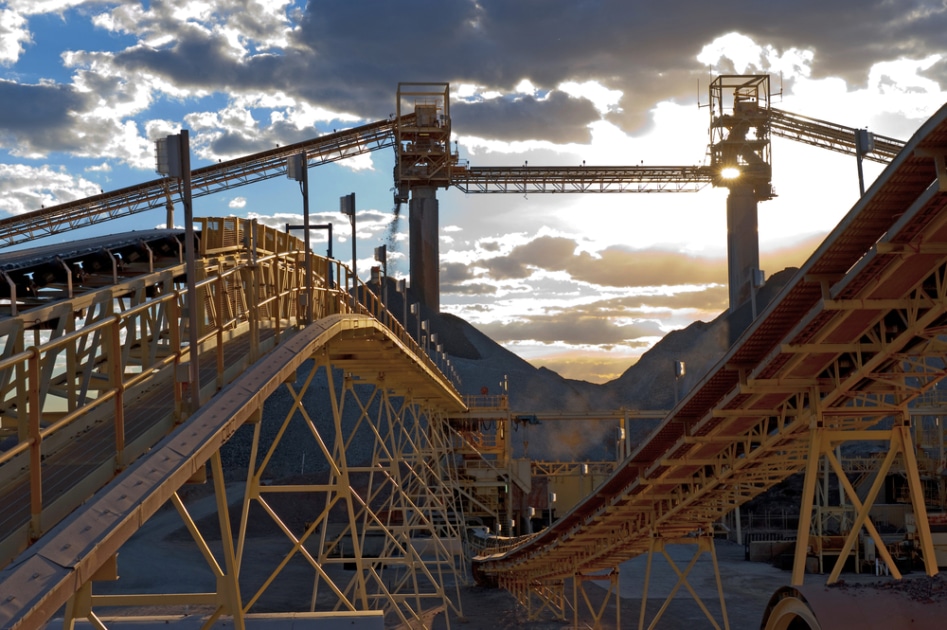
Situation
Conveyor belts are an integral part of the mining and metals industry. Large steel belts transport raw material out of the ground and get it to production. In the metals industry, several kinds of conveyor belts help transport material from one process to another during smelting and other production methods. Because the belts are energy intensive,
they need to be cleaned regularly to ensure energy is managed properly and production is optimal.
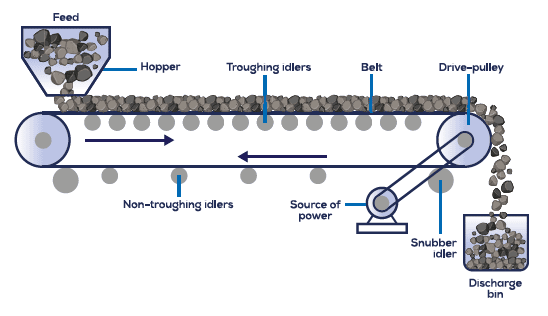
Problem
Engineers at this coal mining operation wanted to learn more about the way its underground conveyor belt used energy. The belt brings coal from the mine to the surface prior to cleaning and transport and is considered the bloodline of the operation. Process experts wanted to change the cleaning schedule from fixed intervals to performance-based in addition to optimizing energy use. To achieve this, they needed to determine the conveyor belt throughput and the relationship between energy usage and the throughput. This would provide the optimal operating point. Once that point was determined, engineers would set up new monitors that would look for deviations from ideal operating parameters. They could use these monitors to schedule maintenance to improve operational and energy efficiency.
Solution
• Create a throughput formula tag based on hopper weight
• Make formula tags for energy used per kilogram of coal transported (specific energy)
• Determine the relationship between the throughput and specific energy consumed
• Set up operating zone monitors to determine when performance drops, which indicates it’s time to clean and perform maintenance
Challenges
Engineers had to calculate the immediate throughput of coal, which is a complication of the process. They also had to filter and clean the data to exclude periods when the conveyor belt was intentionally taken offline for maintenance or other business decisions.
Results
- Process experts were able to identify the optimal throughput for the conveyor belt
- To further optimize energy performance, the hopper control was narrowed
- The new operating zone monitor gives a clear indication of when the conveyor belt needs maintenance
- Engineers can schedule the maintenance when it is necessary to improve operational efficiency, which reduces energy consumption
Situation
Conveyor belts are an integral part of the mining and metals industry. Large steel belts transport raw material out of the ground and get it to production. In the metals industry, several kinds of conveyor belts help transport material from one process to another during smelting and other production methods. Because the belts are energy intensive,
they need to be cleaned regularly to ensure energy is managed properly and production is optimal.
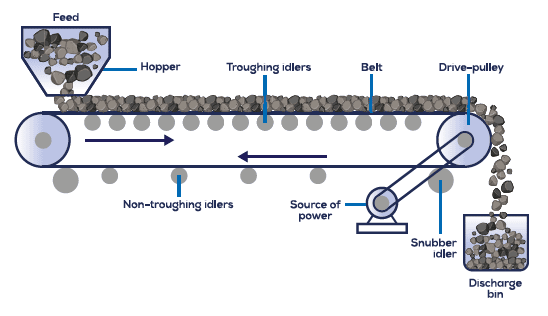
Problem
Engineers at this coal mining operation wanted to learn more about the way its underground conveyor belt used energy. The belt brings coal from the mine to the surface prior to cleaning and transport and is considered the bloodline of the operation. Process experts wanted to change the cleaning schedule from fixed intervals to performance-based in addition to optimizing energy use. To achieve this, they needed to determine the conveyor belt throughput and the relationship between energy usage and the throughput. This would provide the optimal operating point. Once that point was determined, engineers would set up new monitors that would look for deviations from ideal operating parameters. They could use these monitors to schedule maintenance to improve operational and energy efficiency.
Solution
• Create a throughput formula tag based on hopper weight
• Make formula tags for energy used per kilogram of coal transported (specific energy)
• Determine the relationship between the throughput and specific energy consumed
• Set up operating zone monitors to determine when performance drops, which indicates it’s time to clean and perform maintenance
Challenges
Engineers had to calculate the immediate throughput of coal, which is a complication of the process. They also had to filter and clean the data to exclude periods when the conveyor belt was intentionally taken offline for maintenance or other business decisions.
Results
- Process experts were able to identify the optimal throughput for the conveyor belt
- To further optimize energy performance, the hopper control was narrowed
- The new operating zone monitor gives a clear indication of when the conveyor belt needs maintenance
- Engineers can schedule the maintenance when it is necessary to improve operational efficiency, which reduces energy consumption
Download now
Subscribe to our newsletter
Stay up to date with our latest news and updates.
Other Webinars on demand
Explore Our Newest Content to Maximize Your Operational Efficiency
Other Resources
Explore Our Newest Content to Maximize Your Operational Efficiency