Umicore Optimizes Operations and Shift Handover Processes with Analytics
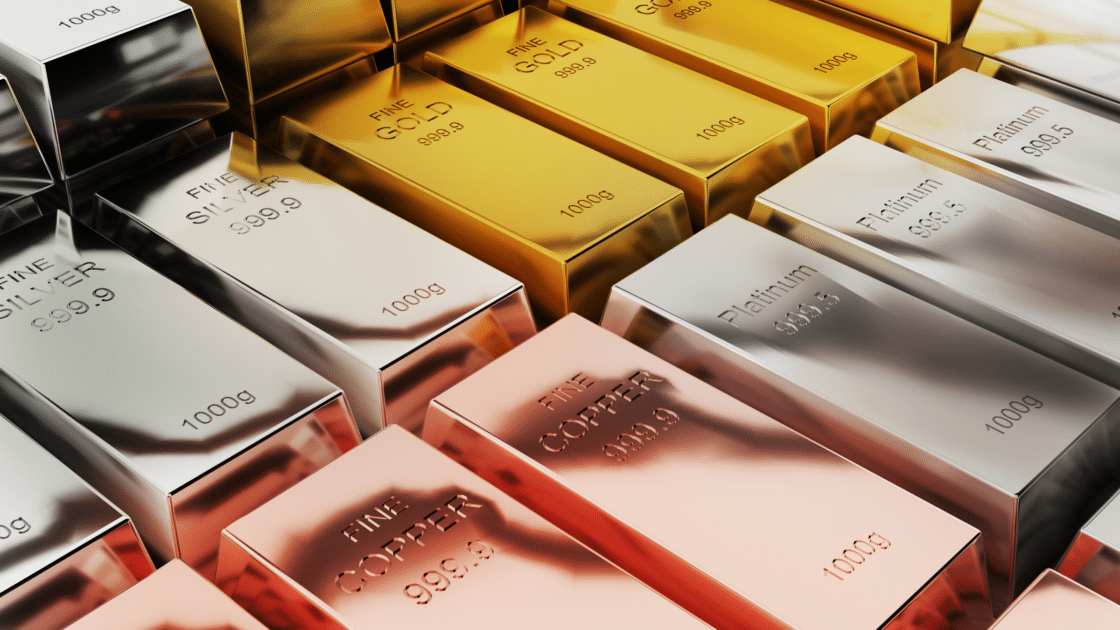
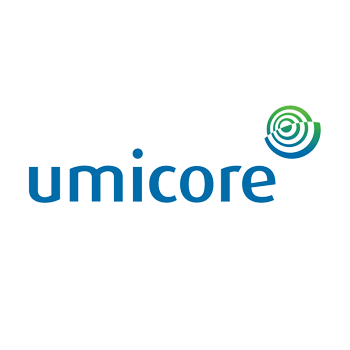
Challenges
- Operational experts lacked access to actionable insights
- Ineffective logging prevented the contextualization of sensor-generated data
- The shift handover between operators was long
Outcomes
- Engineers have the information they need to make data-driven decisions
- The handover time between operators has reduced
- Manufacturing processes show greater stability
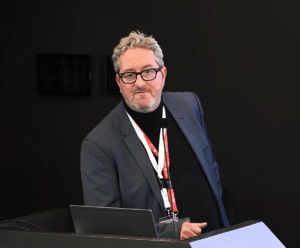
“Through the adoption and use of TrendMiner’s self-service data analytics, Umicore’s operators are now able to analyze process data in context, share dashboards at handovers, exchange analytics with maintenance, and understand where their processes can be adjusted for greater yield and speed. We believe in circularity, with TrendMiner we’ve closed the loop on our data. And it’s in everyone’s hands.”
– Dave Carpels, Sr. Application Analyst at Umicore
Early Data Collection
Umicore might be 135 years old, but it’s just as active as ever. The company processes more than 200 types of raw materials at 500 kt per year. Today, the Belgian company has developed a worldwide reputation for creating sustainable value through the use of “materials for a better life.”
Regardless of its final product, Umicore has always recognized the importance of optimal process behavior to achieve operational efficiency. In the early 1970s, the company began tracking shift data on a single piece of paper. But this proved difficult for analysis because it was not always accurate. For example, if an engineer didn’t log an hourlong lunch break, the runtime for the process might be an hour longer than expected for that shift. Umicore realized by 1995 that it needed to digitalize its operations for more accurate details and better opportunities for analyzing process behavior.
Umicore’s Digitalization Journey
Since Umicore first started its digitalization journey, it has been capturing sensor-generated, time-series data and storing it in an AVEVA PI historian. The company also used AVEVA PI to create asset frameworks and asset templates that log the start and stop times of process events as well as other attributes about them. These insights gave engineers more information than they had before, but it also was becoming more difficult for them to understand the time-series events within their operational context. Furthermore, Umicore wanted to increase its level of analytics maturity and take on more complex use cases. They included diagnostics and predictive and prescriptive insights across multiple assets and simultaneous events.
The company needed a platform to help them democratize data and empower engineers to make data-driven decisions. With TrendMiner, Umicore was able to provide operational experts with a 360-degree view of production. The user-friendly, advanced industrial analytics platform offers a unified view of time-series data within its operational context.
“There were numerous contexts that we wanted greater insight into” Dave said. “From maintenance to visitor requests, temporary changes, to production, consumption and shift handovers—there were so many processes we wanted to begin automating using powerful, reliable analytics.”
Realizing the Value
Since the company deployed TrendMiner in 2022, Umicore has realized a number of benefits from using the advanced industrial analytics platform. They include:
Improved Maintenance
Before Umicore deployed TrendMiner, operators were required to log the abnormalities they discovered and send a request to maintenance to review them. This manual process would take time. “With TrendMiner, process deviation has been automated,” Dave said. “This means maintenance—which uses the tool too—is automatically informed of deviations and a log made in the system that a maintenance request has been made.”
Automating shift handovers
For smoother shift transition, TrendMiner prompts the process engineer to pass any information noted during their shift to their co-worker before they clock out. “These are automatically logged in the system when time-series data is mixed with contextual data and undergoes root cause analysis,” said Dave. “These need to be addressed and discussed before a shift can be officially ended. If a process is supposed to last six hours and an operator completes it in five, the system automatically registers it as a success.”
Streamlining relevant details
Although information is available on TrendMiner’s dashboards, engineers who want more detail will receive an HTML attachment when the shift is handed over to them. This creates a digital audit trail. By tapping into the existing permissions hierarchy within Active Directory, the same privileges to view, edit, and delete items can be extended to TrendMiner users.
“Senior Engineers like me have become experts in data,” said Dave. “But we’re further from the day-to-day reality of our processes. It’s our operators that are the closest to them and now we can give them the intel they need to do their jobs better. Pi enables us to collect and capture our data. TrendMiner empowers us to visualize, analyze, monitor, and predict so we can trigger performance investigations, keep track on contextual events, and make analytics-enabled enhancements. I definitely couldn’t put a number on what value this is unlocking across the production sites where its deployed, but it must be huge.”
Challenges
- Operational experts lacked access to actionable insights
- Ineffective logging prevented the contextualization of sensor-generated data
- The shift handover between operators was long
Outcomes
- Engineers have the information they need to make data-driven decisions
- The handover time between operators has reduced
- Manufacturing processes show greater stability
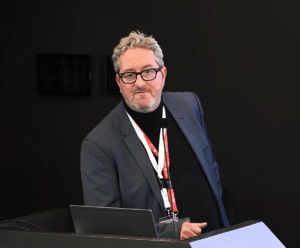
“Through the adoption and use of TrendMiner’s self-service data analytics, Umicore’s operators are now able to analyze process data in context, share dashboards at handovers, exchange analytics with maintenance, and understand where their processes can be adjusted for greater yield and speed. We believe in circularity, with TrendMiner we’ve closed the loop on our data. And it’s in everyone’s hands.”
– Dave Carpels, Sr. Application Analyst at Umicore
Early Data Collection
Umicore might be 135 years old, but it’s just as active as ever. The company processes more than 200 types of raw materials at 500 kt per year. Today, the Belgian company has developed a worldwide reputation for creating sustainable value through the use of “materials for a better life.”
Regardless of its final product, Umicore has always recognized the importance of optimal process behavior to achieve operational efficiency. In the early 1970s, the company began tracking shift data on a single piece of paper. But this proved difficult for analysis because it was not always accurate. For example, if an engineer didn’t log an hourlong lunch break, the runtime for the process might be an hour longer than expected for that shift. Umicore realized by 1995 that it needed to digitalize its operations for more accurate details and better opportunities for analyzing process behavior.
Umicore’s Digitalization Journey
Since Umicore first started its digitalization journey, it has been capturing sensor-generated, time-series data and storing it in an AVEVA PI historian. The company also used AVEVA PI to create asset frameworks and asset templates that log the start and stop times of process events as well as other attributes about them. These insights gave engineers more information than they had before, but it also was becoming more difficult for them to understand the time-series events within their operational context. Furthermore, Umicore wanted to increase its level of analytics maturity and take on more complex use cases. They included diagnostics and predictive and prescriptive insights across multiple assets and simultaneous events.
The company needed a platform to help them democratize data and empower engineers to make data-driven decisions. With TrendMiner, Umicore was able to provide operational experts with a 360-degree view of production. The user-friendly, advanced industrial analytics platform offers a unified view of time-series data within its operational context.
“There were numerous contexts that we wanted greater insight into” Dave said. “From maintenance to visitor requests, temporary changes, to production, consumption and shift handovers—there were so many processes we wanted to begin automating using powerful, reliable analytics.”
Realizing the Value
Since the company deployed TrendMiner in 2022, Umicore has realized a number of benefits from using the advanced industrial analytics platform. They include:
Improved Maintenance
Before Umicore deployed TrendMiner, operators were required to log the abnormalities they discovered and send a request to maintenance to review them. This manual process would take time. “With TrendMiner, process deviation has been automated,” Dave said. “This means maintenance—which uses the tool too—is automatically informed of deviations and a log made in the system that a maintenance request has been made.”
Automating shift handovers
For smoother shift transition, TrendMiner prompts the process engineer to pass any information noted during their shift to their co-worker before they clock out. “These are automatically logged in the system when time-series data is mixed with contextual data and undergoes root cause analysis,” said Dave. “These need to be addressed and discussed before a shift can be officially ended. If a process is supposed to last six hours and an operator completes it in five, the system automatically registers it as a success.”
Streamlining relevant details
Although information is available on TrendMiner’s dashboards, engineers who want more detail will receive an HTML attachment when the shift is handed over to them. This creates a digital audit trail. By tapping into the existing permissions hierarchy within Active Directory, the same privileges to view, edit, and delete items can be extended to TrendMiner users.
“Senior Engineers like me have become experts in data,” said Dave. “But we’re further from the day-to-day reality of our processes. It’s our operators that are the closest to them and now we can give them the intel they need to do their jobs better. Pi enables us to collect and capture our data. TrendMiner empowers us to visualize, analyze, monitor, and predict so we can trigger performance investigations, keep track on contextual events, and make analytics-enabled enhancements. I definitely couldn’t put a number on what value this is unlocking across the production sites where its deployed, but it must be huge.”
Subscribe to our newsletter
Stay up to date with our latest news and updates.
Other Webinars on demand
Explore Our Newest Content to Maximize Your Operational Efficiency
Other Resources
Explore Our Newest Content to Maximize Your Operational Efficiency